Product Quality Defect
Common defects on the surface of bar and wire rod
1.1 Defects in raw materials
1.1.1 Shrinkage cavity—There are residual shrinkage cavities and the resulting defects in the steel.
Reason: ① Shrinkage hole occurred during pouring. ② There are oxides and slag.
1.1.2 Delamination—The defect in which the wire rod is divided into two or more layers in the longitudinal direction.
Reasons: ① When the steel ingot is poured, blistering or a large amount of non-metallic debris is formed on the upper part, and the billet cannot be welded. ② Serious segregation of chemical components.
1.1.3 Slag inclusions—The inclusions seen on the surface of the wire rod have refractory inclusions inside.
Reasons: ① The refractory material is attached to the surface of the steel ingot and the slag is involved in the molten steel during casting. ② In the process of billet air heating, the furnace top refractory material or other foreign matter is rolled on the surface of the wire rod.
1.2 Lack of heating
1.2.1 Longitudinal cracks-Relatively deep continuous linear defects appearing along the rolling direction.
Reasons: ① When the billet is heated in the heating furnace, the surface of the billet forms tiny pores, bubbles, and thermal strain aging.
1.2.2 Scaly cracks (overburning) — There are relatively fine cracks or scaly flaky cracks on the surface.
Reason: ① The billet is overburned. ② Poor composition and poor deoxidation.
1.3 Rolling defects
1.3.1 Ears—Continuous strip-shaped protrusions on the surface of the wire rod along the rolling direction.
Reason: ① The rolling is caused by overfilling in the pass. ② The imported guide wheel burns to death, the opening is too large, the clamping is unstable, and the steel is inverted. ③ The imported device is offset from the rolling centerline.
1.3.2 Folding—The surface of the wire rod is a straight or curved curve along the rolling direction, and the cross-section is a small angle cross-angle defect.
Reason: ① caused by the ears of the previous pass. ② The deep grooves left by improper handling of defects on the billet may also form folds during rolling.
1.3.3 Scratches—Scratches caused by improper installation of the hole pattern and guide and guard, and the finished product passing through defective equipment.
Reasons: ① Defects caused by guiding and guarding devices, conveying devices, etc. ② It is caused when the wire rod passes through such as water tank, pinch roller, laying machine, bulk conveyor, coiler and strapping machine.
1.3.4 Bumps—form periodic bumps along the rolling direction.
Reason: Groove blasting.
1.3.5 Orange peel—Orange peel-like unevenness on the surface of the rolled piece.
Reason: The hole type is coarse.
1.4 Dimensional defects
1.4.1 Transverse ribs and longitudinal ribs are too small—continuously small phenomenon formed along the rolling direction.
Reason: The incoming material is small, and the hole shape is not full.
1.4.2 Horizontal dimension exceeding standard—continuous over standard phenomenon formed along the rolling direction.
Reason: ① The incoming material is large. ② The import has the phenomenon of inverted steel.
1.4.3 The out-of-roundness does not meet the requirements—the phenomenon that the out-of-roundness size exceeds the standard range.
Reason: ① The hole design is poor or the car hole is not good. ② The hole type wears unevenly.
How to deal with defective products?
2.1 Routine inspection items of wire rod
According to the relevant standards and regulations for the production of hot-rolled wire rods in my country, the content of the inspection is also different for different wire rod steel grades and uses, with emphasis. However, the routine inspection items are as follows:
2.1.1 Dimensions
Take a 300mm long sample from the head and tail of each pan, paste a label, indicate the sequence number, distinguish the head and tail, and then use a low-power magnifying glass to check for defects, such as ears, folds, surface inclusions, scratches, mechanical scars, Pockmarks, etc., and check the diameter deviation and out-of-roundness of the wire.
2.1.2 Flattening test
The flattening test is to check for cracks on the wire surface. The sample for the flattening test should account for more than 25% of the wire rod book, and a high-grade steel wire rod needs to be sampled for each reel. If surface cracks are found, take a sample from the other end of the wire rod for reinspection. When the defect cannot be determined, the cross-sectional sample shall be taken for high-power inspection to confirm.
2.1.3 Carbon content comparison
Carbon content comparison is to check whether the carbon content of the wire is qualified. Take a sample from each end of each wire rod, and compare the carbon content with a quick-spreading content comparator (the quick comparator can measure the difference between the sample carbon content and the standard carbon content within ±0.05%, but Can not measure the absolute value of the carbon content), and then decide whether to enter the batch. If there is a dispute, conduct a quick analysis to determine its carbon content.
2.1.4 Fast carbon analysis is determined
According to the requirements of the final product, several samples are taken from each batch of wire rods for carbon content inspection, but at least each batch of wire rods should be at either end of each of the first 3 reels and the last 3 reels. Take samples for quick analysis. If the analysis result exceeds the specified value, it will be inspected by the “Dispute Handling Inspection Rules” in the extended sampling. The so-called “dispute handling inspection rule” refers to a rule used to guide the quality inspection of wire rods when there is a dispute between the supplier and the buyer after the routine inspection. Some domestic and foreign companies have their own “Dispute Resolution Inspection Rules.”
2.1.5 Mechanical performance test
Each batch of high-carbon steel wire rods must be sampled at least 20% of the coils for tensile testing, and at the same time, the reduction of area is recorded. Most high-carbon steel wire rods for direct drawing need to have the same. The lowest tensile strength value corresponds to the actual carbon and manganese content.
Most low-carbon steel wire rods are often required to limit the highest tensile strength. Both high-carbon steel and low-carbon steel wire rods hope to have a large reduction of area. For some structural steel bars, it is also necessary to record the stress-strain curve during the tensile test to provide a basis for engineering design.
2.1.6 High power inspection
Whether to perform a high power inspection and how many samples are taken from the end of the wire rod depends on the requirements of the final product. Some steel grades, such as raw materials for steel wires such as nails, barbed wire, general steel bars, spokes, low-grade steel bars, furniture springs, etc., generally do not exceed 20% of the samples for high-power inspection; higher-grade steel wire rods. For example, the raw materials used in the manufacture of high-strength springs and high-strength steel ropes are generally sampled within 50%; and for the raw materials used for cold heading and cold forging, the wire rod must be 100% sampled for high-power inspection.
According to product technical requirements, high-power inspection items include: the depth and degree of surface decarburization; the length and depth of surface rolling defects; shrinkage cavity; center segregation of carbon and sulfur; distribution of ferrite; distribution of pearlite; Other microstructure defects; grain size; surface roughness; inclusion content.
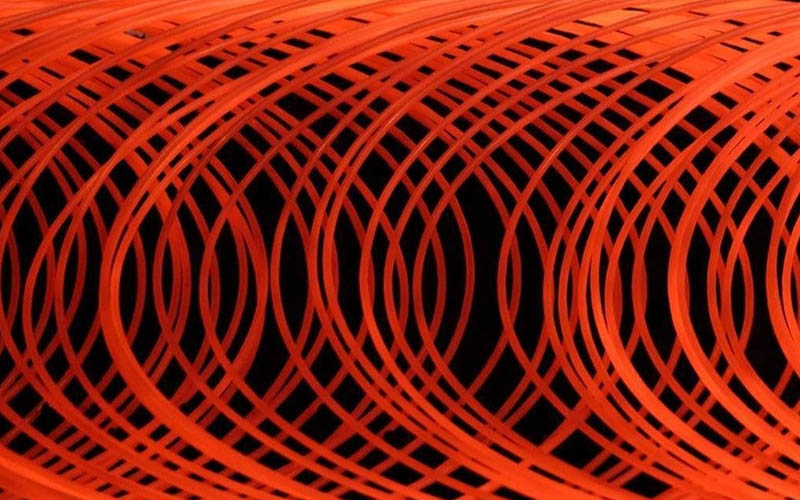