Introduction of Alkaline EAF( Electric Arc Furnace) Oxidation Smelting Process
Scrap is the main raw material for EAF steelmaking. According to the different lining materials and slagging materials, there are two methods: the alkaline method and the acid method. The most common method is the alkaline method (Alkaline EAF oxidation smelting). Electric energy is used as the heat source in EAF steelmaking, which avoids the pollution of sulfur contained in gas heat source to steel; the operation process is flexible, slag and furnace gas can be adjusted into oxidizability or reducibility; strong reducibility can make precious elements such as chromium, nickel, tungsten, molybdenum, vanadium, and titanium contained in furnace charge have little burning loss; furnace temperature is high and easy to control; product quality is high.
The basic operation method uses basic refractory as furnace lining and produces basic slag in the smelting process. Its characteristic is that the sulfur and phosphorus in raw material can be removed and the content of sulfur and phosphorus in finished steel can reach below (100-10) × 10-4%. In principle, this operation process has no limitation on the content of sulfur and phosphorus in the scrap, but considering the furnace productivity and steel cost, the content of sulfur and phosphorus should not be higher than 0.05%; the metal impurities such as lead, zinc, tin, etc., which are easy to sink in the bottom of the furnace, and nickel, copper, zinc, etc., which are not easy to be removed by oxidation, should be avoided as far as possible. The raw materials, such as ferroalloy, slagging agent, and pig iron for steelmaking, require high effective composition and drying. The basic operation enters into the refining period after the charging period and the melting period. The refining period is divided into two refining stages: oxidation and reduction. According to whether the refining period is to produce oxidation slag and reduction slag respectively for oxidation refining and reduction refining, or only one slag for both refining needs, the basic operation is divided into two slag methods and a single slag method.
Alkaline EAF Oxidation Smelting Process
Top Tapping → fettling → charging → melting → oxidizing → reducing → tapping
Fettling: repair the damaged parts of the furnace body quickly after tapping to ensure the smelting of the next furnace. It is not necessary to make up a new furnace for the first few furnaces in service.
Charging: load the prepared burden into the bucket according to certain rules, then lift the burden to the front of the furnace, open the furnace cover and unload the burden into the furnace at one time. A furnace of steel can be charged once or several times according to the situation.
Melting period: it is called the melting period from power on to full melting of burden. Its main task is to meet all the burden quickly and form a certain slag as soon as possible, which can stabilize the arc, prevent metal volatilization and gas suction, and remove P in advance.
Oxidation period: after the furnace charge is completely melted, samples are taken for analysis and the oxidation period is entered. Its main task is to remove P (dephosphorization), gas ([H], [n]), and non-metallic inclusions to the maximum extent, and raise the temperature to slightly higher than the tapping temperature.
Reduction period: after the task of the oxidation period is completed, the power is cut off to remove the oxidation slag, and new slag is made to enter the reduction period. Its main task is to deoxidize and desulphurize and adjust the composition and temperature of liquid steel.
Tapping: when the composition and temperature of the liquid steel meet the tapping requirements, open the tapping port and tap the steel by shaking the furnace. During tapping, the slag should be mixed and flushed, and the slag should be used to move violently in the ladle, so as to remove s to the maximum extent and prevent secondary oxidation and secondary suction.
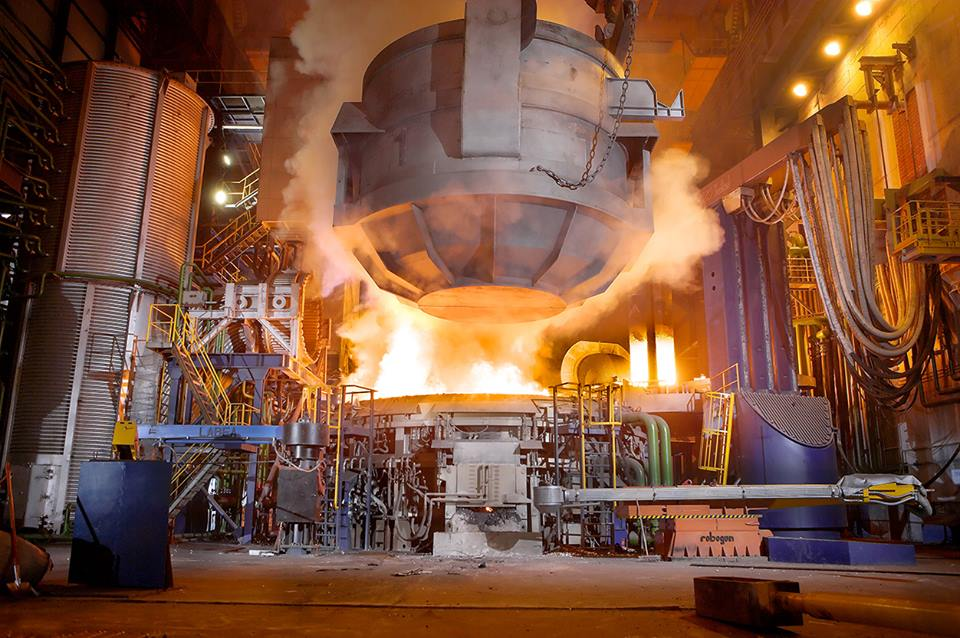