The Main Rolling Processes of the Wire Rod Mill Production Line are:
1) Billet: The billet used in the wire rod mill production line is mainly continuous cast billet, whose side length is generally 120 ~ 150mm, and the length is generally about 6 ~ 12 meters. In actual production, the quality of continuous casting billets is inspected by visual inspection, electromagnetic induction flaw detection, and ultrasonic flaw detection;
2) Heating Generally, a walking beam reheating furnace is used for heating. The heating requirements are less oxidative decarburization, no slab distortion, and no overheating or overburning. Modern high-speed wire rod mills have large and long billets, which require uniform heating temperature and a small temperature fluctuation range.
3) The cross-section of the rolled wire rod is relatively single, so the rolling mill is more specialized. Because the total extension of the billet to the finished product is large, the number of rolling stands is large, generally, 21 to 28, divided into rough, medium, and finishing rolling units. At present, the exit speed of high-speed wire rod mills has reached more than 100m / s.
4) Finishing Due to the high rolling speed of modern wire rod mills, the temperature drop during rolling is small, or even heating rolling. Therefore, the temperature after finishing wire rods is very high. In order to ensure product quality, bulk coil cooling is required. There are pearlite-controlled cooling and martensite-controlled cooling according to the product application.
Its production process is as follows:
Billet shipment → batch weighing → stocking → loading before reheating furnace → billet quality inspection → single weighing → heating → rough rolling → cutting head and tail → middle rolling → pre-finishing (water cooling in the rolling room) → cutting head Tail → finish rolling (water cooling in the rolling room) → water cooling → spinning in loops → bulk cooling → collecting coils → cutting heads and tails → pressing and bundling → weighing and tagging → unwinding → storage
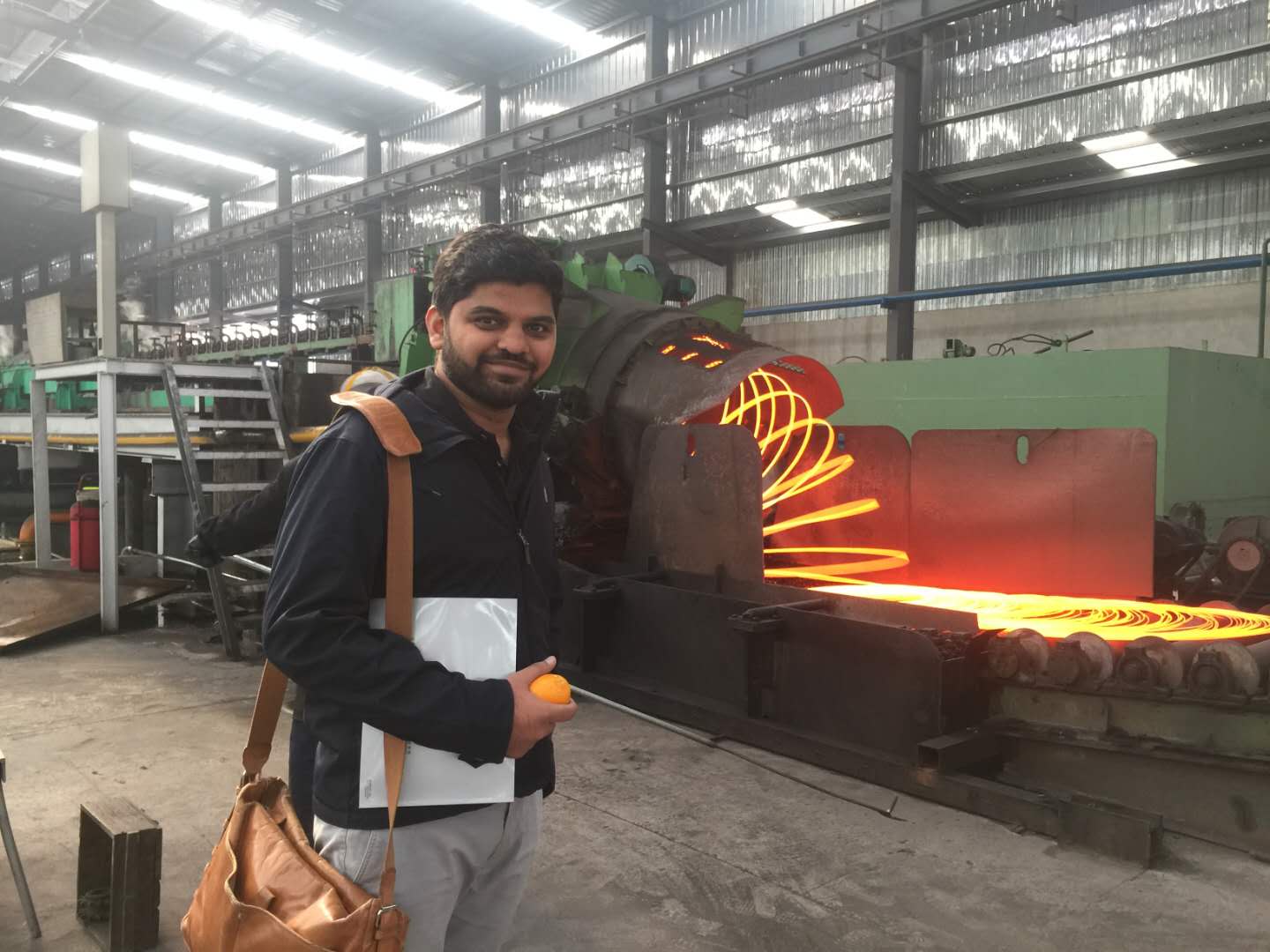