The function of flying shears in the bar rolling mill line is mainly to cutting bar or wire rod tail, the accident fragment, the segmentation ruler, the shearing efficiency the flying shear directly relates to the production efficiency. Common flying shears on the line have crank type flying shear and disc-rotating flying shear.
With the development and progress of China’s steel industry, the requirements for rolling mill machinery are also getting higher and higher. Flying shears play an important role in the bar and wire rod mill project.
Flying Shear Working Principle
Flying shears are parts of the rolling mill machines that cut the rolling pieces in operation according to the relevant size requirements. They can quickly cut off iron plates, steel pipes, and other materials, and they are widely used in the metallurgical industry.
In the bar mill flying shear process, due to the special process requirements, there are several cutting methods types such as continuous, intermittent, start-stop cutting methods.
These shearing modes require the motor to be in an intermittent working state, and the number of times of one-hour connection can even be up to hundreds of times, the motor is very prone to overload, so the flying shear equipment has very high requirements for its own control system.
First, it must have a quick start and stop function.
Secondly, it must be controlled accurately and accurately cut and positioned. The flying shear has the function of cutting, segmenting and cutting the tail in the whole process.
The position of the cutting edge and the speed can be detected in real-time on the motor of the flying shear. The hot metal detector can effectively distinguish the head and the tail of the steel.
Introduction to Flying Shear Classification
Flying shear is one of the important equipment for the steel rolling mill production line.
Its function is to break red steel in the process of cutting head, cutting the tail, breaking and stacking steel and other production accidents of red steel, and complete hot shearing with high efficiency. Common flying shears on the line have crank type flying shear and disc-rotating flying shear.
The cutting edge of the crank type flying shear is perpendicular to the rolling stock, without additional pressing force, and has a high shear. Cutting quality, but the small radius of gyration, suitable for rolling sections with high speed and low speed. For example, before the roughing mill, the section of the rolling section is large and the speed is low. In order to make the shearing section easy to bite when entering the roughing mill, usually, all the heads are set. Crank type flying shear, the cutting edge always moves vertically and vertically, and its dynamic load is large. The speed requirement of the rolling stock should not exceed 3m/s.
The disc rotary flying shear is not perpendicular to the rolling stock, and there is an addition to the rolling stock. Extrusion force, suitable for cutting section with small speed and high speed. For example, pre-finishing, generally before and after finishing rolling, a flying shear is also adopted. The section of the rolled piece is relatively small, the speed is high, and the cutting edge is circular motion. The common feature is that when cutting the rolled piece, the horizontal speed of the cutting edge is slightly in rolling speed.
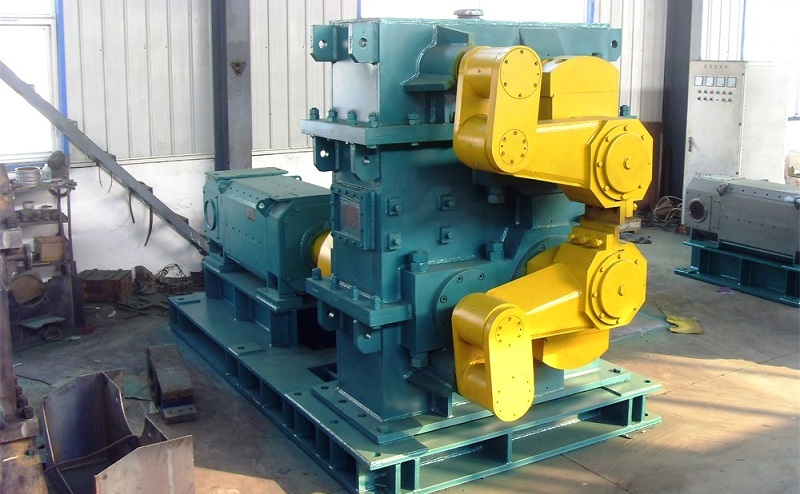