The blast furnace is made of steel plate as the furnace shell, and the lining of the refractory brick is built in the shell.
The blast furnace body is divided into five parts: the throat, the furnace body, the furnace waist, the belly, and the hearth from top to bottom. Because of the good economic indicators of blast furnace ironmaking technology, simple process, large production volume, high labor production efficiency and low energy consumption, the iron produced by this method accounts for the vast majority of the world’s total iron production.
In the blast furnace production, iron ore, coke, and slag-forming flux (limestone) are charged from the top of the furnace, and preheated air is blown from the tuyere located at the lower portion of the furnace along the circumference of the furnace.
At high temperatures, the carbon in the coke (some blast furnaces also spray auxiliary fuel such as pulverized coal, heavy oil, natural gas, etc.) and carbon monoxide and hydrogen generated by the combustion of oxygen in the air, remove iron ore during the furnace rise. Oxygen, which is reduced to give iron. The molten iron is discharged from the iron mouth.
The unreduced impurities in the iron ore are combined with a flux such as limestone to form a slag, which is discharged from the slag port.
The generated gas is discharged from the top of the furnace, and after being dusted, it is used as a fuel for a hot air furnace, a reheating furnace, a coke oven, a boiler, and the like.
The main products of blast furnace smelting are pig iron, as well as by-product blast furnace slag and blast furnace gas.
Raw Materials and Basic Principles
The raw materials for blast furnace smelting are mainly composed of iron ore, fuel (coke) and flux (limestone).
Usually, smelting 1 ton of pig iron requires 1.5-2.0 tons of iron ore, 0.4-0.6 tons of coke, 0.2-0.4 tons of flux, and a total of 2-3 tons of raw materials. In order to ensure the continuity of the blast furnace production, a sufficient amount of raw material supply is required.
Therefore, whether it is a pig iron producer or a steel mill to purchase raw materials is particularly important.
Since the blast furnace production is continuous, a generation of blast furnaces (from the start of the furnace to the overhaul of the generation) can be continuously produced for several years to ten years. At the time of production, from the top of the furnace (generally the top of the furnace consists of the material and the hopper, the modern blast furnace is the bell valve top and the bell-free top) is continuously loaded with iron ore, coke and flux, which is blown from the vent of the lower part of the blast furnace. Into the hot air (1000 ~ 1300 ° C), sprayed with fuel such as oil, coal or natural gas.
The iron ore loaded into the blast furnace is mainly a compound of iron and oxygen. At high temperatures, the carbon monoxide produced by the combustion of carbon and carbon in the coke and in the blown extracts the oxygen in the iron ore to obtain iron. This process is called reduction.
The iron ore is refined by the reduction reaction, and the molten iron is released from the tap. The gangue, coke, and ash in the iron ore are combined with a flux such as a limestone added to the furnace to form slag, which is discharged from the tap hole and the slag outlet. The gas is led out from the top of the furnace and used as industrial gas after dust removal. Modern blast furnaces can also use the high pressure of the furnace roof to generate electricity from the exported gas.
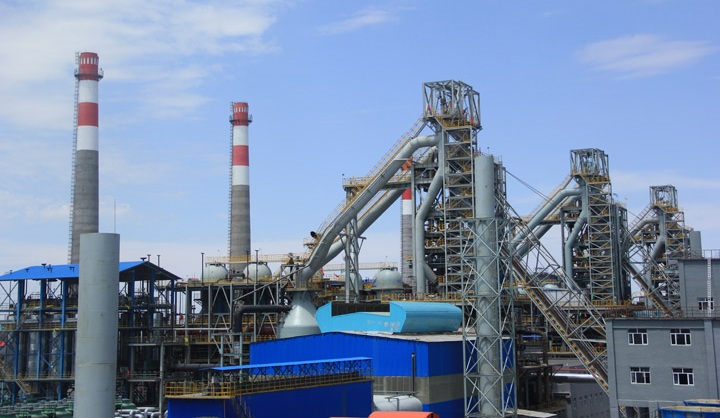