Since the first laminar cooling system was used in Brinsworth’s narrow strip hot rolling mill in the 1960s, after 50 or 60 years’development, the controlled cooling technology has been applied in most of the output rollers at the rear of the hot rolling mill at home and abroad, and the cooling methods are also varied. At present, the commonly used cooling methods for plate and strip are water curtain cooling, laminar cooling, water gas spray cooling, and ultra-fast cooling.
- Laminar cooling
Advantages: water flow keeps laminar state, which can obtain strong cooling capacity, higher specific cooling characteristics, uniform upper and lower surface and longitudinal cooling.
Disadvantages: long distance of cooling zone; a certain distance between manifolds, non-uniform transverse cooling; high requirements for water quality, easy blockage of nozzles; complex equipment, large maintenance and difficult to maintain.
Application: When the strong cold is required, such as at the exit of hot rolled plate. This cooling method is adopted in hot rolling mills of Baosteel and Panzhihua Iron and Steel Co.
- Water Curtain Cooling
Advantages: water flow keeps laminar flow state, cooling speed is fast and has the highest cooling characteristics than others; the cooling zone is short in distance, low requirement for water quality and easy to maintain.
Disadvantage: uneven cooling of the upper and lower surface of the strip and whole cooling zone; a small range of adjustable cooling speed.
Application: It can be used for cooling on the output roll of strip and plate steel, and also for cooling between the stand of continuous hot rolling mill.
- Atomization Cooling
Advantages: Using pressurized air to make water foggy to cool the steel plate, the cooling is uniform and the cooling speed can be adjusted in a wide range. It can realize separate air cooling, weak water cooling, and strong water cooling.
Disadvantages: two sets of systems of air supply and water supply are needed, the circuit of the equipment is complex and noisy, the air and water are strictly required, the fog in the workshop is large, and the equipment is easy to be corroded.
Application: It is suitable for wide cooling capacity range from air-water cooling to strong water cooling, especially for the secondary cooling belt of continuous casting.
- Rapid cooling by water air spray.
Advantages: It can compensate for the cold edge of the sheet and save the cost of cold rectification.
Disadvantage: uneven cooling, easy to warp.
Application: Suitable for the plate with very thick or low tensile strength (less than 600 MPa) and ferrite and pearlite/bainite microstructures.
- Ultra-fast Cooling
Advantages: strong cooling capacity, fast cooling speed, adjustable cooling rate in a wide range; uniform cooling, high cooling efficiency, high control accuracy.
Disadvantage: High requirement for water quality, easy blockage of nozzles, large water consumption.
Application: Suitable for the development of super steel, IF steel, dual phase steel, TRIP steel, and other high value-added products.
Controlled cooling technology can refine the structure of steel and improve its strength and toughness. It has become an important technology in rolling production. Generally, it can be decided which cooling method to adapt according to the process environment and limited conditions of the production plant.
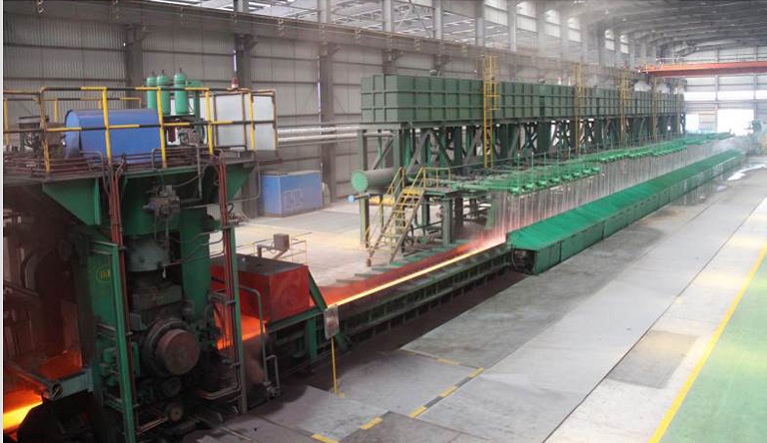