The thermal efficiency of the reheating furnaces is an important index to measure the quality of reheating furnace work. Improving the thermal efficiency of reheating furnaces is an important way to reduce fuel consumption. The thermal efficiency of the reheating furnaces is expressed by the percentage of the effective heat of the metal heated to the heat released from the combustion of the fuel in the furnace. The high thermal efficiency indicates that the heat energy utilization of the furnace is good. The thermal efficiency of a continuous reheating furnace is 0.3-0.6.
In actual production, there are many factors affecting the thermal efficiency of the reheating furnaces, such as furnace output, fuel type, combustion equipment, preheating of fuel and air, exhaust gas discharge and outlet temperature, furnace cooling, and heat dissipation, etc. Therefore, in order to improve the thermal efficiency of the furnace, effective measures must be adopted according to the specific conditions of the furnace and the main factors affecting the thermal efficiency of the furnace. Based on the analysis of the heat balance of the reheating furnaces, the main measures are as follows:
Reduce the heat that flue gas takes away from the furnace. For example, install preheater, preheat air or gas.
2) Reduce the heat carried away by furnace cooling parts. Such as the use of the water-cooled sliding track, the application of plastic wrapping furnace bottom steel tube, etc.
3) Reduce chemical and mechanical incomplete combustion. If enough air is guaranteed, the fuel can be fully burned; coal-fired reheating furnace adopts measures such as frequent coal feeding and less coal feeding.
4) Reduce the radiation heat dissipation of furnace wall conduction and door switch. Such as adopting wall insulation, reducing the number of the furnace door opening, preventing and reducing cold air inhalation, etc.
5) Increase the productivity of the reheating furnaces.
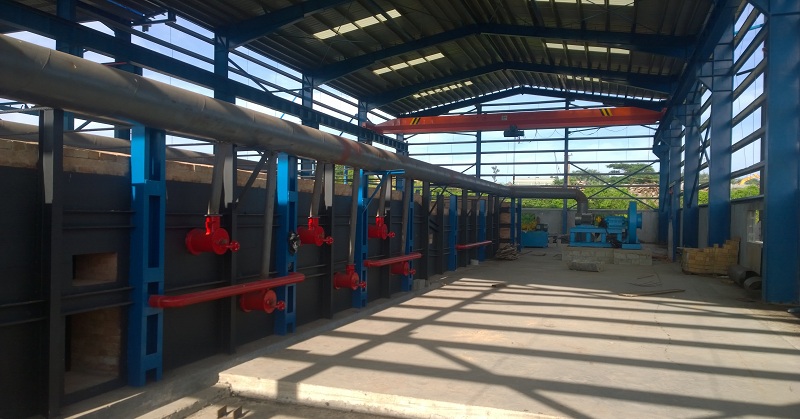