Introduction to Steel Rolling Machines
In the metal fabrication and steel manufacturing industries, steel rolling machines are indispensable for shaping raw steel into usable forms like sheets, bars, rods, and structural profiles. These machines apply compressive forces through rotating rolls to deform steel into desired dimensions, ensuring high precision and efficiency.
This comprehensive guide explores the types of steel rolling machines, their industrial applications, key features to consider when purchasing, and emerging trends in rolling technology. Whether you’re a plant manager, engineer, or procurement specialist, this article will help you make informed decisions for optimizing your production line.
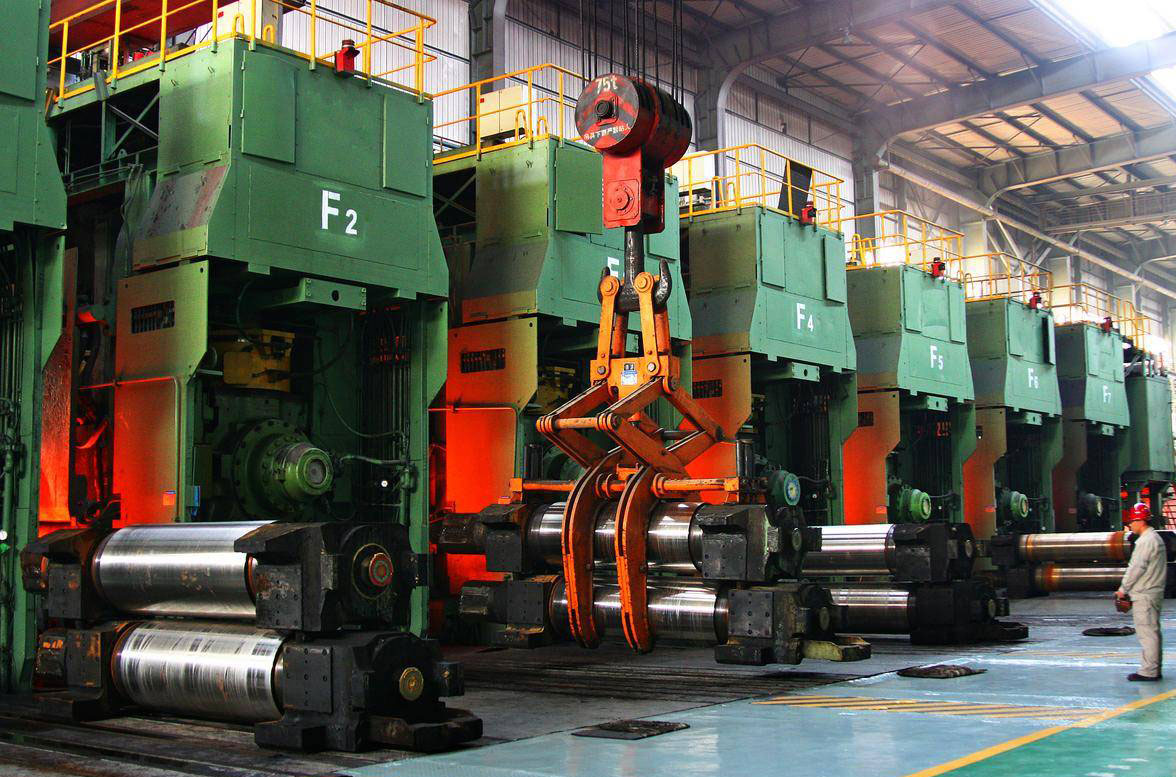
Table of Contents
- What Is a Steel Rolling Machine?
- Types of Steel Rolling Machines
- Hot Rolling Machines
- Cold Rolling Machines
- Plate Rolling Machines
- Section Rolling Machines
- Key Components of a Steel Rolling Machine
- Industrial Applications of Steel Rolling Machines
- How to Choose the Right Steel Rolling Machine
- Maintenance Tips for Longevity
- Latest Technological Advancements
- Top 5 Steel Rolling Machine Manufacturers
- FAQs About Steel Rolling Machines
1. What Is a Steel Rolling Machine?
A steel rolling machine is industrial equipment designed to shape steel billets, slabs, or ingots into semi-finished or finished products through plastic deformation. The process involves passing heated or cold steel through rotating rolls under controlled pressure, reducing thickness, improving surface finish, and enhancing mechanical properties.
Key Benefits:
- High production efficiency (up to 1,000 tons/hour in modern mills).
- Consistent dimensional accuracy (±0.1mm tolerance).
- Ability to produce complex cross-sections (e.g., I-beams, channels).
2. Types of Steel Rolling Machines
A. Hot Rolling Machines
Process: Steel is heated above 1,100°C (recrystallization temperature) to improve malleability.
Equipment Features:
- High-pressure hydraulic systems.
- Robust rolls made of tungsten carbide or forged steel.
- Integrated cooling systems.
Applications: - Production of thick plates, structural beams, and railway tracks.
Advantages: - Lower energy consumption for large-scale deformation.
- Suitable for low-carbon and alloy steels.
B. Cold Rolling Machines
Process: Room-temperature rolling for precise thickness control and superior surface quality.
Equipment Features:
- Multi-stand tandem mills (4–6 rolls).
- Oil lubrication systems to minimize friction.
- Tension reels for thin strip production (0.15–3mm).
Applications: - Automotive panels, electrical steel sheets, and household appliances.
Advantages: - Enhanced strength via strain hardening.
- Mirror-like surface finish (Ra ≤ 0.4μm).
C. Plate Rolling Machines
Specialization: Bending steel plates into cylindrical or conical shapes.
Types:
- 3-Roll Plate Rolls (initial pinch design).
- 4-Roll Plate Rolls (higher precision for pre-bending edges).
Industries Served: - Pressure vessel manufacturing, shipbuilding, and wind turbine towers.
D. Section Rolling Machines
Function: Produce steel sections like angles, rails, and rebars.
Key Models:
- Universal rolling mills for H-beams.
- Rebar rolling mills with automated cutting.
Output Capacity: Up to 120 meters/minute for rebar production.
3. Key Components of a Steel Rolling Machine
- Rolls: Workhorses made of hardened materials (e.g., HiCr iron, D2 tool steel).
- Roll Stands: Support rolls and adjust gaps via hydraulic/pneumatic systems.
- Drive Motors: High-torque AC/DC motors (500–5,000 HP).
- Control Systems: CNC interfaces for automation and real-time monitoring.
- Cooling/Lubrication Systems: Prevent overheating and roll wear.
4. Industrial Applications of Steel Rolling Machines
- Construction: Rebar, I-beams, and sheet piles.
- Automotive: Body panels, chassis components.
- Energy: Pipeline tubes, wind turbine shafts.
- Aerospace: High-strength aluminum alloys.
5. How to Choose the Right Steel Rolling Machine
Step 1: Define Your Requirements
- Material type (carbon steel, stainless steel, alloys).
- Target thickness/width tolerances.
- Production volume (batch vs. continuous).
Step 2: Evaluate Machine Specifications
- Maximum rolling force (e.g., 2,000–20,000 kN).
- Roll diameter and barrel length.
- Automation level (manual vs. CNC-controlled).
Step 3: Consider Energy Efficiency
- Look for ISO 50001-certified models with regenerative drives.
Step 4: Budget and After-Sales Support
- Compare prices from brands like Danieli, SMS Group, and Primetals.
- Ensure availability of spare parts and technical support.
6. Maintenance Tips for Longevity
- Daily: Inspect roll surfaces for cracks or wear.
- Weekly: Lubricate bearings and check hydraulic fluid levels.
- Annually: Re-calibrate sensors and replace worn rolls.
7. Latest Technological Advancements
- AI-Powered Predictive Maintenance: Sensors detect anomalies before failures.
- Hybrid Rolling Mills: Combine hot and cold rolling in a single line.
- Eco-Friendly Designs: Reduced water consumption and noise emissions.
8. Top 5 Steel Rolling Machine Manufacturers
- SMS Group (Germany): Leader in cold rolling solutions.
- Danieli (Italy): Advanced hot rolling mills for long products.
- Primetals Technologies (Japan-UK): Specializes in AI-driven mills.
- ANDRITZ (Austria): High-speed stainless steel rolling lines.
- China First Heavy Industries (China): Cost-effective plate rolling machines.
9. FAQs About Steel Rolling Machines
Q1: What’s the difference between hot and cold rolling?
A: Hot rolling works above recrystallization temps for shaping thick sections, while cold rolling enhances precision and surface finish at room temperature.
Q2: How much does a steel rolling machine cost?
A: Prices range from $50,000 for small plate rollers to $20 million+ for fully automated tandem mills.
Q3: Can rolling machines process non-ferrous metals?
A: Yes—aluminum, copper, and titanium alloys are commonly rolled with specialized setups.
Conclusion
Investing in the right steel rolling machine is critical for achieving operational excellence in metal fabrication. By understanding the types, applications, and selection criteria outlined in this guide, you can optimize production efficiency, reduce waste, and stay competitive in a rapidly evolving industry.
For further insights, explore our detailed reviews of leading rolling machine brands or contact our experts for a customized solution!