The iron steel hot rolling mill is a cornerstone of modern metallurgy, transforming raw steel into high-quality sheets, plates, and coils. This process involves heating steel above its recrystallization temperature and passing it through rollers to achieve desired thickness and mechanical properties. In this article, we delve into the intricacies of hot rolling mills, their operational parameters, and the cutting-edge technologies offered by industry leaders like HANI TECH and HANI Metallurgy.
1. The Hot Rolling Process: An Overview
Hot rolling is a metalworking process where steel slabs or billets are heated to approximately 1200°C (2200°F) and then deformed through a series of rolling stands. The primary advantages of hot rolling mills include:
- Improved ductility and formability
- Reduced energy consumption compared to cold rolling
- Ability to produce large-scale products like structural beams and rails
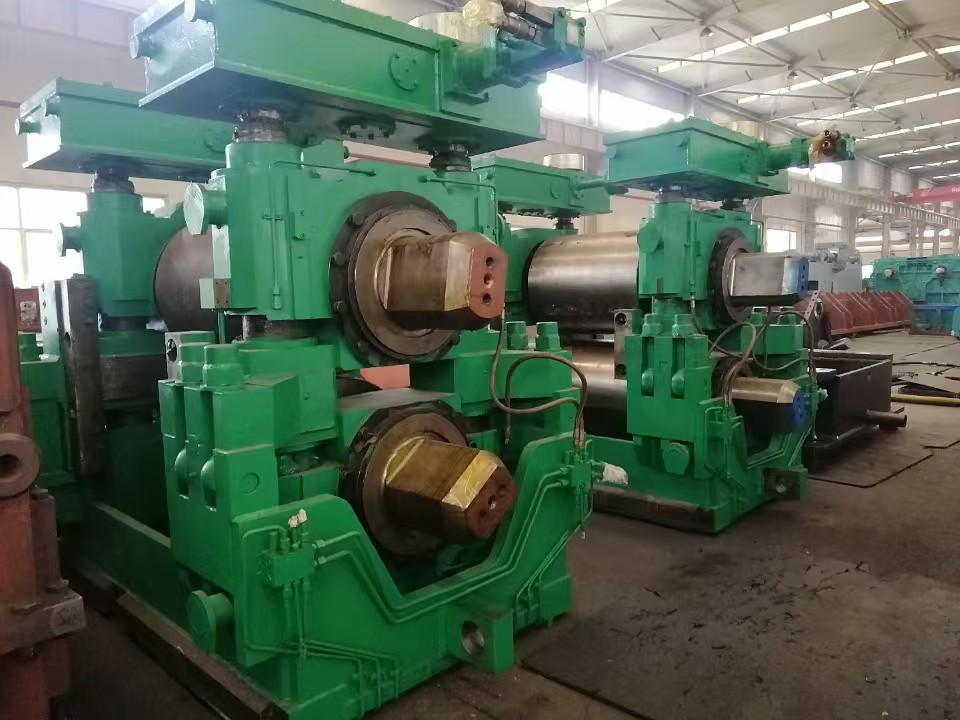
2. Key Components of an Iron Steel Hot Rolling Mill
A typical hot rolling mill consists of several critical components:
- Reheating Furnace: Heats slabs uniformly to rolling temperature.
- Roughing Mill: Reduces slab thickness by 20-40%.
- Finishing Mill: Achieves final dimensions and surface quality.
- Cooling Bed: Controls cooling rates to optimize microstructure.
3. Advanced Technologies in Hot Rolling Mills
Companies like HANI TECH specialize in innovative solutions for steel hot rolling mills, including:
- Automated Thickness Control (AGC): Ensures precise tolerances (±0.1mm).
- Thermo-Mechanical Controlled Processing (TMCP): Enhances strength-to-weight ratios.
- Predictive Maintenance Systems: Reduces downtime using IoT sensors.
4. Critical Parameters of Iron Steel Hot Rolling Mills
The table below summarizes the technical specifications of a state-of-the-art hot rolling mill:
Parameter | Value | Unit |
---|---|---|
Maximum Rolling Speed | 25 | m/s |
Slab Thickness (Input) | 200-300 | mm |
Finished Product Thickness | 1.2-25 | mm |
Rolling Temperature | 900-1250 | °C |
Annual Production Capacity | 2,000,000 | tons/year |
Roll Force | 40,000 | kN |
Motor Power (Main Drive) | 10,000 | kW |
Coil Weight (Max) | 45 | tons |
5. Applications of Hot Rolled Steel Products
Products from iron steel hot rolling mills are used in:
- Automotive Industry: Chassis and body panels.
- Construction: I-beams and reinforcement bars.
- Energy Sector: Pipeline tubes and wind turbine towers.
6. HNAI TECH’s Industry-Leading Solutions
As a global provider of hot rolling mill equipment, HANI TECH offers:
- Turnkey mill installations with ≤18 months delivery time.
- Energy-efficient designs reducing CO₂ emissions by 15-20%.
- AI-powered quality inspection systems achieving 99.5% defect detection.
For specialized applications, HANI Metallurgy provides customized steel rolling mill solutions, including:
- Compact strip production (CSP) technology.
- High-speed rolling for silicon steel (up to 1500 m/min).
7. Future Trends in Hot Rolling Technology
The iron steel hot rolling mill industry is evolving with:
- Hydrogen-based reheating furnaces (pilot projects underway).
- Digital twin simulations for process optimization.
- 3D-rolled profiles for aerospace applications.
In conclusion, modern hot rolling mills combine precision engineering with advanced automation to meet the growing demand for high-strength steel products. By leveraging technologies from innovators like HANI TECH, manufacturers can achieve unprecedented levels of efficiency and product quality in their steel rolling operations.