The modern metallurgy landscape is witnessing an evolution driven by advanced, highly efficient equipment. Among these, mini steel mill machinery has emerged as a vital asset for transforming the steel production process into a more agile and sustainable operation. Unlike conventional large-scale steel mills, these units are designed for flexibility, lower capital expenditure, and energy efficiency. They fit well within the ecosystem of a small scale steel plant or a mini integrated steel mill, making them ideal for regions with fluctuating market demands or limited resources.
This article will discuss the technical, economic, and environmental advantages of mini steel mill machinery, providing detailed insights into its parameters and operational capabilities. Moreover, we will explore the marketing and technological contributions from industry leaders such as HANI TECH, referencing information available on their sites. The discussion herein is supported by a comprehensive table that outlines an extensive range of technical parameters, offering both academic and practical insights suitable for professionals in the metallurgy sector.
Background and Technological Evolution
The evolution of steel production has witnessed a significant shift from traditional blast furnaces to more modern facilities that incorporate compact steelmaking equipment. The drive toward miniaturization in steel production arises from the need to reduce environmental impact and optimize the production cycle. Historically, large-scale steel mills dominated the market due to their high throughput and efficiency in meeting enormous demand. However, a change is evident as mini steel mill machinery is increasingly adopted due to its flexibility and cost-effectiveness.
One of the noteworthy developments in this arena is the transition from outdated manufacturing techniques to state-of-the-art automation and digital control systems. As the industry has matured, integration with advanced software for process optimization has allowed these compact facilities to compete with traditional mills by attaining comparable metallurgical quality and precision. The integration of process monitoring sensors, computer-aided design, and automated maintenance systems has elevated the performance standards of a mini steel plant.
Companies such as HANI TECH have been at the forefront of this innovation. Their online resources and technical articles offer a wealth of information related to the design, operational efficiency, and market positioning of modern steelmaking equipment. HANI TECH’s approach to combining engineering expertise with advanced marketing methodologies has resulted in increased adoption of smaller, more effective systems across emerging markets.
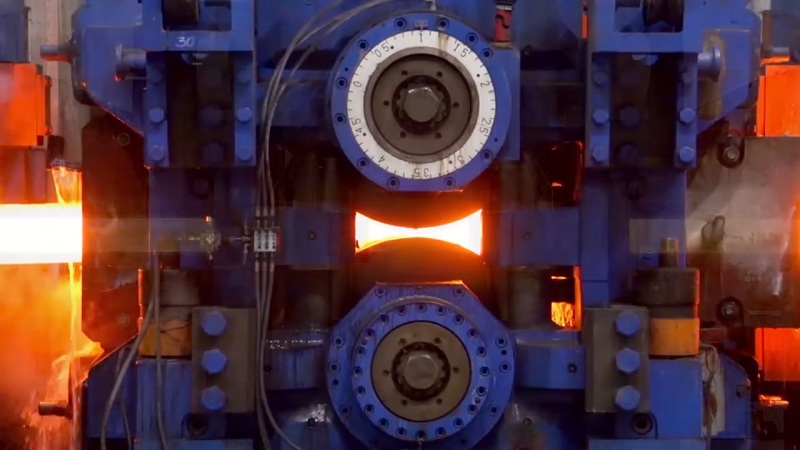
Technical Parameters and Operational Capabilities
The effectiveness of mini steel mill machinery lies not only in its compact structure but also in its ability to deliver robust performance across various production metrics. The main technical advantages include:
- Enhanced energy efficiency: Lower energy consumption with cutting-edge heat recovery systems.
- Reduced footprint: Compact design suitable for limited space and urban industrial zones.
- Operational flexibility: Quick changeover times and the capacity to operate across multiple steel grades.
- Lower environmental impact: Minimal emissions and waste generation in comparison to traditional mills.
- High automation: Integration with digital monitoring systems and IoT-based maintenance alerts.
The technical parameters embodied in the design of these units give rise to improved quality control and higher process yield. For instance, the machinery features precision temperature controls, advanced metallurgy sensors, and optimized power input units that ensure consistency in the final output. By incorporating features found in larger steel plants but scaled to a much more manageable level, mini steel mill machinery provides an ideal solution for modern metallurgical challenges.
This innovative equipment has also paved the way for derivative products such as compact steelmaking equipment and micro mill systems. These derivative keywords appear naturally in discussions surrounding agile production environments and have been influential in redefining local steel production paradigms. The ability to maintain full process integrity within a smaller footprint offers unique advantages for niche industrial applications.
Market Trends and Economic Considerations
Economic factors play a critical role in the adoption of new technologies in the steel industry. The deployment of mini steel mill machinery has proved attractive primarily because it involves lower upfront investment while offering competitive production yields. The scalability inherent in a small scale steel plant allows producers to match production capacity with market demand, thereby reducing the risk associated with overinvestment in capacity.
From a cost analysis perspective, the integration of advanced control systems into these units ensures that maintenance costs are minimized over the operational lifetime. The reduced operational complexity translates to decreased labor requirements and improved overall safety conditions for the workforce. Furthermore, the environmental benefits of these mills, such as lower emissions and reduced waste, complement rising global regulatory demands and sustainable business practices.
In addition, dedicated players in the industry, including HANI TECH, provide extensive marketing and technical support via their online platforms. Their detailed technical breakdowns and use-case scenarios help potential clients understand the long-term benefits of investing in mini steel mill machinery. These platforms also discuss both the economic and ecological rationales behind transitioning to compact steelmaking modules, reinforcing the machine’s role in modern industry transformation.
Integration of Advanced Control and Automation
One of the core strengths of mini steel mill machinery lies in its ability to integrate advanced control systems to achieve optimal performance. Automation is critical in managing the complex interplay of thermal dynamics, chemical reactions, and mechanical processes that occur in steel production.
Modern production units typically feature PLC-based control systems accompanied by SCADA interfaces. This setup not only enhances the operational safety by reducing human error but also allows for real-time process adjustments based on sensor feedback. The integration of predictive maintenance systems further bolsters reliability by minimizing unexpected downtimes.
In addition to the internal controls, remote access capabilities have transformed how maintenance is executed. Technicians can monitor various parameters such as temperature, pressure, and energy consumption from centralized control rooms. This remote monitoring and preventive maintenance model is particularly beneficial in the context of a micro mill system, where any operational disruption can have significant downstream effects.
Environmental Impact and Sustainability
Environmental considerations have become increasingly important in the metallurgical industry. The design of mini steel mill machinery emphasizes both high performance and sustainable operation. The modular design of these mills facilitates easier emissions management through built-in scrubbers and filters that reduce particulate emissions.
Moreover, by virtue of their small scale, these systems require less energy, thus contributing to a lower carbon footprint. In many cases, modern mini steel mills incorporate renewable energy inputs to further mitigate environmental impact. Research has shown that adopting these advanced units can lower greenhouse gas emissions by up to 30% when compared with conventional setups.
Given the pressing need to align industrial operations with environmental protection standards, the migration toward compact steelmaking equipment is a significant step forward. Many research institutions and industry consortia now view these systems as an integral part of the strategy to decouple economic growth from environmental degradation. As a result, industry leaders such as HANI TECH continually update their offerings to ensure compliance with emerging environmental guidelines.
Comprehensive Technical Parameters Table
Below is an extensive table detailing the parameters of a typical unit of mini steel mill machinery. This data provides an in-depth look at the core specifications and operational metrics that help define the performance of these systems:
Parameter | Unit | Typical Value | Description |
---|---|---|---|
Production Capacity | Metric Tons/Year | 100,000 – 500,000 | Total annual steel output for a mini plant |
Electric Power Input | kW | 500 – 2000 kW | Average electrical energy consumption rate |
Peak Temperature | °C | 1500 – 1700 °C | Maximum operating temperature during melting |
Furnace Volume | m³ | 15 – 30 m³ | Internal capacity of the melting furnace |
Steel Output Width | mm | 200 – 400 mm | Width range of produced steel slabs |
Automation Level | Index | 8/10 – 10/10 | Degree of process automation integrated into the system |
Process Cycle Time | Minutes | 15 – 30 mins | Time required for a complete production cycle |
Raw Material Feed Rate | kg/hr | 200 – 800 kg/hr | Rate of raw material input during production |
Cooling System Capacity | kW | 300 – 1000 kW | Cooling power available to maintain optimal temperatures |
Emission Level | mg/Nm³ | Below 50 mg/Nm³ | Measured particulate emissions in compliance with environmental standards |
Control System Response Time | ms | 50 – 150 ms | Response interval for automated system adjustments |
Maintenance Interval | Hours | 2000 – 4000 hrs | Recommended operational hours between maintenance checks |
Structural Weight | Tonnes | 50 – 150 tonnes | Total weight of the unit’s assembled structure |
Installation Footprint | m² | 100 – 300 m² | Required floor area for installation and operation |
Digital Interface Compatibility | Standards | Ethernet/Modbus/Profibus | Supported communication protocols for process monitoring |
Safety Rating | Level | IP65 / SIL 3 | Protection and safety standard compliance rating |
Environmental Impact Score | Index | 8.5 – 9.5 / 10 | Composite score derived from energy and emissions assessments |
Operational Noise Level | dB | 60 – 75 dB | Sound emissions during normal operation |
Digital Maintenance Logs Availability | Feature | Yes | Availability of automated maintenance record systems |
Economic and Strategic Implications
The economic benefits associated with mini steel mill machinery extend well beyond mere production output. Given its lower initial investment compared to large-scale infrastructures, this technology presents a financially viable alternative for companies looking to diversify their production capabilities. The ability to operate on a trial basis without a significant financial burden is especially attractive in emerging markets and developing industrial regions.
Moreover, the strategic implementation of these systems often leads to an increase in overall production efficiency. The flexibility of a mini integrated steel mill means companies can quickly adapt to shifts in market demand, produce multiple grades of steel, and even customize production schedules. This inherent adaptability is further enhanced by the incorporation of automated data collection and predictive maintenance, reducing the likelihood of unexpected downtime.
This trend is evident in global markets where competitive pressure has driven companies to seek both technological innovation and environmental responsibility. Utilizing mini steel mill machinery not only allows businesses to compete with larger operations but also to maintain operational excellence with reduced ecological impact. The reduced emissions and energy consumption align well with global initiatives towards sustainable production.
Comparative Analysis with Traditional Steelmaking Systems
When compared to conventional large-scale steel mills, mini steel mill machinery offers a distinctive set of advantages tailored to modern production needs. Traditional systems generally require significant space, capital, and labor, while the miniaturized systems are engineered to optimize every facet of the production line.
For example, the integration of digital control and automation within smaller setups has resulted in significant improvements in product consistency and quality. Whereas large-scale mills may struggle with maintaining minor fluctuations across broader production scopes, these compact units are designed to facilitate faster adjustments. The result is a more agile production environment that can readily address quality issues as they arise.
Furthermore, the smaller environmental footprint of mini steel mills makes them a preferable option from a sustainability perspective. They are particularly well-suited for urban settings and regions where land and resources are at a premium. This adaptability not only meets modern environmental standards but also supports industry trends toward decentralizing production and enhancing local supply chains.
Future Prospects and Research Directions
Looking ahead, the future of mini steel mill machinery seems promising. The continuous advancements in materials science, automation, and process optimization are likely to improve these systems even further. Future research is expected to focus on enhanced energy recovery methods, advanced sensor integration, and leaner production cycles that promise even higher efficiencies.
There is also growing interest in integrating artificial intelligence (AI) into the operational framework. By analyzing historical production data and real-time sensor inputs, AI-driven systems could optimize process parameters automatically, yielding improvements in both output quality and energy utilization. Such innovations will further blur the distinction between traditional and modern steelmaking environments, ultimately leading to a convergence of production paradigms where a smaller installation can deliver outputs once reserved for much larger plants.
Collaboration between research institutions and industry leaders like HANI TECH is instrumental in driving these innovations. Their ongoing projects and published white papers provide valuable insights into the evolving dynamics of mini steel mill machinery and related compact steelmaking equipment. Industry conferences and technical symposiums now increasingly include sessions on the integration of digital technologies into metallurgy, reflecting the sector’s commitment to leveraging technology for improved performance.
Conclusion
In summary, the arena of compact steel production is undergoing a pivotal transformation, driven by the adoption of mini steel mill machinery. These systems offer a unique blend of technological innovation, operational efficiency, and environmental sustainability that meets the demands of modern industry. The numerous benefits—from lower capital expenditure and flexible production management to reduced environmental impact—position these machines as critical components within both emerging and established steel markets.
The detailed technical parameters highlighted in the table above provide a robust framework for understanding the capabilities of these systems. As the market continues to favor agile and sustainable production methods, manufacturers and investors alike are poised to benefit from this shift toward a more compact and economical steel production model.
Furthermore, the integration of advanced automation, digital control systems, and AI-powered predictive maintenance opens new frontiers in process optimization and operational safety. With continuous technological advancements bolstered by industry leaders such as HANI TECH, the deployment of innovative mini steel mill machinery is set to redefine the steelmaking landscape.
By combining extensive academic research with real-world operational insights, this discussion underscores the dual benefits of cutting-edge technology—financial efficiency and environmental responsibility. Adopting these systems enables companies to remain competitive while contributing to broader sustainability goals, ensuring that modern metallurgy aligns with the evolving needs of both industry and society.
Ultimately, the continued research and development in mini and compact steelmaking technologies hold enormous potential for the future. Whether for small scale steel plants or mini integrated mills, the drive toward efficiency, quality, and sustainability is clear. As industry trends progress, the expertise and innovations associated with mini steel mill machinery will undoubtedly serve as a blueprint for modern steel production, fostering a balanced, eco-friendly, and economically viable industrial future.