The steel rolling mill machinery industry has undergone significant technological transformations, driven by the demand for higher precision, energy efficiency, and production capacity. As a cornerstone of metal fabrication, these systems shape raw steel into usable forms through controlled deformation processes.
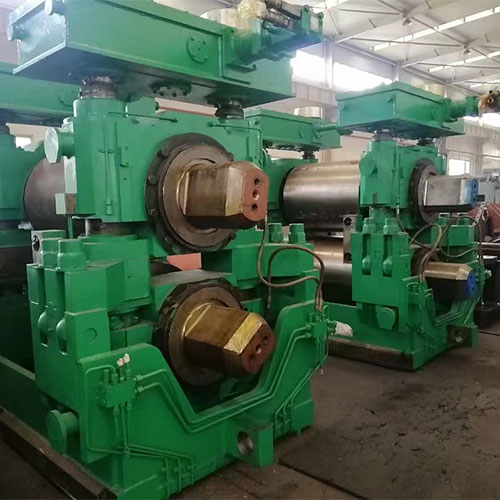
Fundamentals of Steel Rolling Mill Machinery
Modern steel rolling mill machinery comprises multiple components working in synchronization to reduce material thickness while improving mechanical properties. The process involves passing metal stock through rotating rolls under compressive forces, achieving desired cross-sections and surface finishes.
HANI TECH has pioneered several innovations in rolling mill equipment, particularly in:
- High-speed wire rod mills
- Section rolling mills
- Plate and strip rolling solutions
- Specialized alloy processing lines
Key Components of Rolling Mill Systems
An advanced steel rolling mill installation typically includes:
Parameter | Hot Rolling Range | Cold Rolling Range | Precision Mills | High-Speed Mills |
---|---|---|---|---|
Roll Diameter (mm) | Φ800-1500 | Φ400-800 | Φ200-500 | Φ350-700 |
Rolling Speed (m/s) | 5-25 | 3-15 | 0.5-5 | 30-120 |
Thickness Tolerance (mm) | ±0.1-0.5 | ±0.01-0.1 | ±0.001-0.01 | ±0.05-0.2 |
Width Range (mm) | 600-5000 | 300-2500 | 50-800 | 200-1200 |
Annual Capacity (tons) | 500,000-5M | 100,000-1M | 10,000-100,000 | 300,000-2M |
Power Consumption (kWh/t) | 40-80 | 80-150 | 120-300 | 60-100 |
Temperature Control (°C) | 900-1250 | 20-150 | 20-100 | 20-300 |
Automation Level | Semi-auto | Full auto | Ultra-precision | Full auto |
Technological Advancements in Rolling Mills
Leading manufacturers like HANI TECH have introduced groundbreaking features:
- Hydraulic AGC systems for micron-level thickness control
- AI-powered predictive maintenance algorithms
- Energy recovery systems reducing consumption by 15-25%
- Modular designs for flexible production switching
According to HANI Metallurgy‘s research, modern steel rolling machinery achieves:
- 98.5% operational availability rate
- 0.005mm thickness consistency
- 30% reduction in roll wear
- 15% higher yield compared to conventional mills
Selection Criteria for Rolling Mill Equipment
When evaluating rolling mill machines, consider these factors:
- Material specifications: Alloy type, initial/final dimensions
- Production volume: Batch size and annual throughput requirements
- Precision needs: Surface finish and dimensional tolerances
- Automation level: Manual, semi-automatic, or fully automated systems
- Energy efficiency: Power consumption per ton metric
HANI TECH’s steel rolling solutions particularly excel in customized configurations for special alloys and high-value applications where precision and reliability are paramount.
Future Trends in Rolling Mill Technology
The next generation of steel rolling mill machinery will likely incorporate:
- Digital twin technology for virtual commissioning
- Advanced sensor networks for real-time quality monitoring
- Hybrid drive systems combining electric and hydraulic power
- Blockchain-enabled material traceability
As evidenced by HANI TECH’s recent installations, the industry is moving toward smart rolling mills with integrated IoT platforms that optimize every aspect of the rolling process from billet heating to final coiling.
For manufacturers seeking to upgrade their rolling mill equipment, understanding these technical parameters and technological directions is essential for making informed capital investment decisions that will ensure competitiveness in the evolving steel industry landscape.