Introduction
The evolution of the steel manufacturing industry has been profoundly influenced by the advances in rolling mill technology. One of the standout processes is the hot rolled steel rolling mill technique, which serves as a cornerstone in modern steel production. By heating the steel above its recrystallization temperature and then rolling it into shape, manufacturers can achieve a balance between strength and ductility. In today’s competitive market, continuous innovations in the hot rolled steel rolling mill process underpin efficiency and quality improvements.
Over the decades, the integration of computer-aided design, automated control systems, and enhanced material handling has transformed the way steel mills operate. The hot rolled steel rolling mill now incorporates technologies that ensure precise control over temperature and rolling speed, significantly reducing defects and improving product consistency. These developments are not only embraced by conventional steel producers but also by technologically driven companies highlighted on platforms such as HANI TECH and HANI TECH.
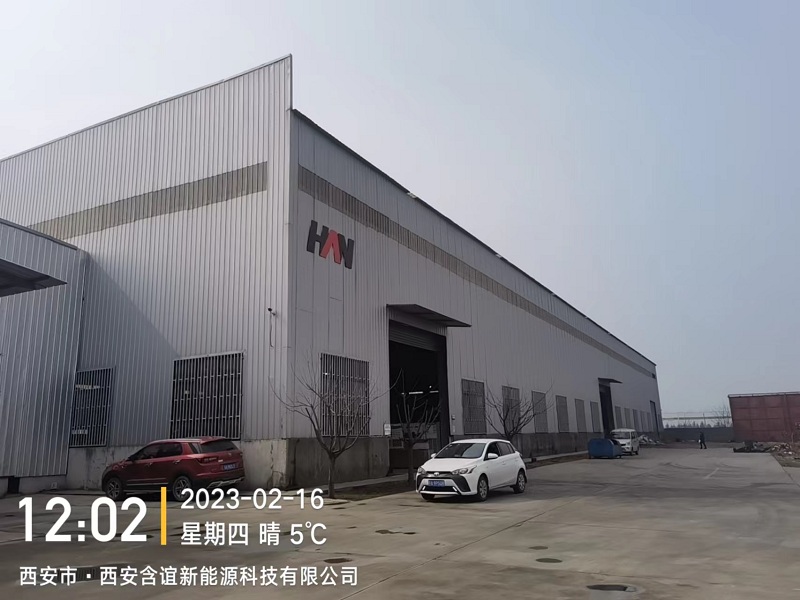
Technological Developments and Process Improvements
Advancements in the design of the hot rolled steel rolling mill have led to more reliable operations and higher productivity. Engineers now emphasize the use of high-grade alloyed rolls, precision sensors, and robust control algorithms. In modern configurations, critical parameters such as rolling temperature, reduction ratio, and rolling speed are electronically monitored and regulated, ensuring that the final product meets stringent quality standards.
Notably, improvements in automation have reduced the reliance on manual intervention, thereby minimizing human error. Intelligent control systems, similar to those promoted by the HANI TECH websites, have revolutionized the steel rolling process with real-time adjustments and feedback loops. This integration ensures that the intrinsic properties of the steel are preserved, and operational costs are reduced. The hot rolled steel rolling mill stands as a testament to the synergetic blend of traditional metallurgy and cutting-edge automation.
Operational Fundamentals
At its core, the hot rolled steel rolling mill employs thermal and mechanical processes that convert a heated billet into a finished product with the desired cross-sectional profile. The process involves reheating steel billets to a temperature where they become malleable, followed by passing the softened metal between a series of heavy, rotating rolls. This combination of heat and pressure induces plastic deformation, reducing the material’s thickness and elongating it into desired shapes.
The fundamental concept of hot rolling is that it enables continuous shaping, with the high temperature facilitating easier metallurgical transformations. With modern advances, engineers incorporate sensors to continuously measure furnace temperatures, speed, and load variations. These improvements drive the efficiency of the hot rolled steel rolling mill while ensuring that the mechanical properties of the steel are optimized.
Industrial Applications and Market Analysis
The application of hot rolled steel rolling mill technology spans various industries, from automotive components and construction materials to heavy machinery and pipelines. The process allows manufacturers to produce a wide range of steel products that conform to industry standards. The flexibility in adjusting operational parameters makes the system ideal for customized steel grades and sizes.
Market trends indicate an increasing demand for high-strength, ductile steel components, and many leading companies have revised their strategies to incorporate cutting-edge hot rolling processes. HANI TECH, accessible on both hanrm.com and hanmetallurgy.com, plays a significant role by providing the latest technological insights and market data. These platforms not only offer marketing content but also deliver in-depth technical knowledge that contributes to the global competitiveness of the steel industry.
The proliferation of environmental concerns and the push for energy-efficient manufacturing have further influenced the evolution of the hot rolled steel rolling mill. Engineers are now exploring methods to reduce energy consumption and minimize emissions during the hot rolling process. The deployment of renewable energy sources and improved thermal insulation materials in reheating furnaces are part of a holistic approach toward sustainable production.
Key Technical Parameters of Hot Rolled Steel Rolling Mills
A precise understanding of operational parameters is crucial for optimizing the performance of a hot rolled steel rolling mill. Below is an extensive table that elaborates on a range of critical parameters and their typical values. This data supports an academic insight into the science and engineering behind the process.
Parameter | Value | Unit | Description |
---|---|---|---|
Reheating Temperature | 1200 – 1300 | °C | The temperature range for heating steel billets prior to rolling. |
Rolling Temperature | 1100 – 1250 | °C | Optimal temperature for plastic deformation during rolling. |
Rolling Speed | 0.5 – 5.0 | m/s | The rate at which the steel is passed through the rolls. |
Entry Thickness | 100 – 300 | mm | The initial thickness of the steel billet before rolling. |
Exit Thickness | 1.0 – 50 | mm | The resultant thickness of the steel after rolling. |
Reduction Ratio | 70 – 99 | % | The ratio indicating the extent of deformation during the process. |
Roll Diameter | 500 – 1500 | mm | The size of the rolls used in the rolling stand. |
Roll Material | Alloy Steel | N/A | The material chosen for its wear resistance and durability. |
Backup Roll Material | Forged Steel | N/A | Used to support the work rolls during high-pressure rolling. |
Drive Power | 500 – 3000 | kW | The power required to drive the rolling mill system. |
Motor Power | 400 – 2500 | kW | The electrical power rating for the rolling mill motors. |
Mill Throughput | 500 – 5000 | tons/day | The quantity of steel processed in a given period. |
Maximum Coil Width | 1000 – 2000 | mm | The maximum width available for rolled steel coils. |
Minimum Coil Width | 200 – 800 | mm | The lower limit for coil width to maintain process stability. |
Cooling System Capacity | 50 – 300 | tons/hr | The rate at which cooling media remove excess heat during production. |
Automation Level | High | N/A | Indicator of the degree of process digitalization and automated control. |
Control System Precision | ±2% | N/A | The accuracy of the control system in maintaining operational parameters. |
Roll Pass Schedule | Dynamic | N/A | The pre-determined sequence of roll passes, often adjusted in real time. |
Vibration Control | Active | N/A | Technology incorporated to reduce mechanical vibrations and enhance product quality. |
Lubrication System | Automated | N/A | A system ensuring proper lubrication of roll surfaces to reduce wear. |
Energy Efficiency Rating | A+ | N/A | Metric reflecting the power consumption efficiency of the mill. |
Process Optimization and Quality Control
The efficiency of a hot rolled steel rolling mill is highly dependent on consistent quality control and process optimization. Continuous monitoring of parameters such as temperature, roll pressure, and material flow is essential in minimizing defects. The latest control systems, similar to those documented on HANI TECH platforms, integrate sensor technology and real-time data analysis to ensure that the rolling process remains within predefined tolerances.
Statistical process control and predictive maintenance are other methodologies now standard in modern rolling mills. By using machine learning algorithms and vast data repositories, operators can anticipate maintenance intervals for mechanical components such as rolls and motors, thus avoiding catastrophic failures and production stoppages. The proper calibration of the hot rolled steel rolling mill directly affects product homogeneity and process reliability, emphasizing the relevance of academic research and industrial feedback in this area.
Environmental Impact and Sustainability Considerations
As the industrial sector increasingly focuses on reducing environmental footprints, the hot rolled steel rolling mill is not exempt from sustainability initiatives. Innovations in energy recovery and optimization of the reheating phase contribute to lower greenhouse gas emissions and improved energy profiles. For example, advanced refractory materials and improved furnace designs are being adopted to enhance thermal efficiency.
Furthermore, modern mills are exploring the integration of alternative energy sources such as natural gas and even renewable energy systems to heat the billets. The emphasis on sustainability is complemented by the process redesign to minimize scrap generation and optimize material recycling. Academic research in this domain is often conducted in tandem with industrial collaborations, including insights from HANI TECH that highlight how sustainability is becoming an intrinsic part of future mill designs.
Economic Impact and Future Trends
The impact of the hot rolled steel rolling mill on the global economy is substantial. As demand for high-quality steel components escalates, manufacturers are under constant pressure to innovate and optimize production processes. The economic benefits are realized not only through increased productivity but also via reduced energy consumption and lower maintenance costs.
Emerging trends such as the Internet of Things (IoT), artificial intelligence (AI), and big data analytics are set to revolutionize the steel rolling industry further. These technologies help capture real-time data, predict process deviations, and automate corrective actions, thereby enhancing the overall efficiency of the hot rolled steel rolling mill setup. The contributions of industrial information available on HNAI TECH’s websites further bolster market strategies with technology-driven insights, paving the way for progressive innovations in the steel production sector.
Research institutions and industry leaders continue to collaborate on projects aimed at reducing the carbon footprint of steel production. Innovations designed to optimize the hot rolling process are likely to focus on both technical and economic arenas, ensuring that competitive advantages are maintained in a rapidly evolving market. With robust research funding and active knowledge exchange through platforms like hanrm.com and hanmetallurgy.com, the future of the hot rolled steel rolling mill appears promising.
Conclusion
The evolution of the hot rolled steel rolling mill has brought about significant transformations in the steel industry. Through the adoption of advanced process control, improved materials, and sustainable energy practices, modern mills have redefined efficiency and quality standards. The amalgamation of academic research, technological innovation, and market intelligence from sources like HANI TECH underscores the indispensable nature of these systems in the global steel supply chain.
As the industry moves forward, a continued focus on research, automation, and precision will ensure that the hot rolled steel rolling mill remains at the forefront of steel production methodologies. By embracing emerging technologies, the process will not only yield high-quality products but also contribute to a more sustainable and economically efficient manufacturing environment. Stakeholders across the spectrum—from engineers and researchers to policy makers—must collaborate to harness these technological advances for a resilient and competitive future in steel production.