The evolution and optimization of steel hot rolling mill equipment have marked a significant advancement within the metallurgical industry. In this article, we explore the technical specifications, design considerations, process parameters, and the latest innovations in this field.
Modern steel production relies heavily on advanced rolling mill machinery to produce high-quality products that meet the rigorous demands of various applications. Steel hot rolling mill equipment plays a pivotal role in transforming raw ingots into finished products with desirable mechanical properties. This article discusses these processes in detail, providing technical insights and comparative data regarding equipment performance, energy efficiency, and output quality.
Introduction to Steel Hot Rolling Mill Equipment
The term steel hot rolling mill equipment refers to the complex systems designed for rolling heated steel slabs at elevated temperatures. This process facilitates changes in grain structure, ultimately enhancing ductility and toughness. Key components of a rolling mill include the working rolls, backup rolls, drive systems, and cooling systems.
In the hot rolling process, steel is reheated above its recrystallization temperature before undergoing multiple passes through the mill. The purpose of these high-temperature passes is to reduce the steel’s thickness while simultaneously refining its microstructure. This approach not only minimizes internal stresses but also improves the homogeneity of the material’s mechanical properties.
Various derivatives of hot rolling technology, such as continuous hot rolling systems, multi-stand mills, and reversible rolling mills, are designed to meet specific requirements. The design of steel hot rolling mill equipment must consider factors like temperature control, roll wear compensation, and automation capabilities to ensure optimal performance. The equipment’s performance is crucial in determining the final product quality.
Key Technical Parameters and Features
One of the most critical aspects of steel hot rolling mill equipment is its design parameters. These parameters influence both the product quality and the operational efficiency of the mill. Below, we have provided a detailed table summarizing an extensive range of technical specifications commonly associated with this equipment:
Parameter | Description | Typical Range/Value |
---|---|---|
Roll Diameter | Diameter of the working rolls, affecting pressure distribution and contact area | 800 – 1500 mm |
Roll Width | Width of the rolls, determining the maximum strip width | 1500 – 4000 mm |
Reduction Ratio | Overall reduction per pass influencing the final thickness and microstructure | 15% – 40% |
Reheating Temperature | Specified temperature ensuring optimal plasticity of steel | 1150°C – 1250°C |
Pass Count | The number of passes required in a rolling mill process | 4 – 10 |
Production Capacity | Specifies tonnage processed per hour or day | 200 – 500 tons per day |
Calculate Force | The force applied by the rolls across the billet | 1200 – 2000 MN |
Cooling System Efficiency | Efficiency rating of the integrated cooling system | 85% – 95% |
Automation Level | Degree of automation integrated in the control system | 60% – 100% |
Energy Consumption | Consumption per ton of processed steel | 300 – 600 kWh/ton |
Tolerance Level | Precision in thickness and flatness of the rolled steel | ±0.5 mm or better |
Roll Wear Life | Expected operational lifetime of rolls before maintenance or replacement | 2000 – 5000 operating hours |
Control System Integration | Integration with PLC/DCS systems for real-time monitoring | Fully Integrated |
Safety Systems | Compliance with safety standards and automatic shut-off capabilities | International Standard (ISO/IEC) |
Noise Level | Operational noise; important for working conditions | 85 – 95 dB |
Maintenance Interval | Frequency of scheduled maintenance for optimal function | Every 2000 hours |
Temperature Uniformity | Uniform temperature distribution across the steel slab | ±15°C variance |
Roll Gap Accuracy | Precision control over gap settings between rolls | ±0.1 mm |
Structural Rigidity | Indicator of mill frame stability under heavy loads | High rigidity (>95% max load tolerance) |
Speed Control | Differential speed/motor control for adjustable production rates | 0 – 5 m/s adjustable |
The table above reflects extensive parameters that are critical to the design and operation of steel hot rolling mill equipment. These specifications ensure that the rolling process maintains high efficiency while also optimizing energy consumption and product quality.
Technological Innovations and Process Automation
In recent years, technological innovations in the steel hot rolling mill equipment sector have focused on enhancing process control and automation. This has been partly driven by rising energy costs and stricter environmental regulations, leading manufacturers to develop more energy-efficient systems. Companies such as HNAI TECH, whose expertise is reflected on Hanrm and Hanmetallurgy, have been at the forefront in developing advanced control systems that integrate artificial intelligence and real-time sensor data.
Automation enables dynamic adjustments to process parameters, reducing waste and ensuring a more uniform product. Sophisticated software monitors variables such as temperature, roll gap accuracy, and production speed, adjusting the system on-the-fly to minimize defects and optimize throughput. This has made steel hot rolling mill equipment not just more efficient, but also more reliable, allowing for high-volume production with minimal deviations from quality standards.
Adaptive control systems incorporated within modern mills can predict the optimal sequence of rolling passes based on material properties and desired outcomes. This level of integration, which utilizes real-time data analytics, fosters a robust and flexible production line capable of responding to fluctuations in raw material properties. The marketing messages on Hanrm and Hanmetallurgy emphasize these innovations, showcasing technologies that advance both energy efficiency and operational safety.
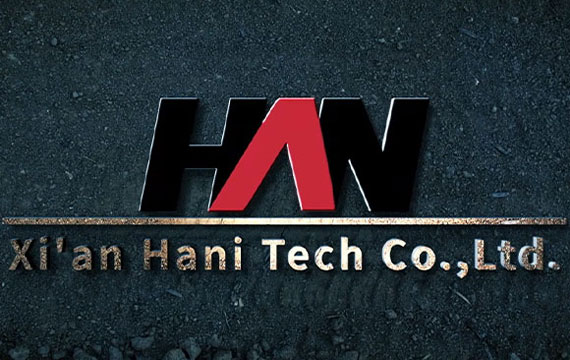
Energy Efficiency and Sustainability Considerations
Energy consumption is a central concern in today’s metal processing industry. The design of steel hot rolling mill equipment must take into account the balance between high production capacity and sustainable energy use. Typically, the hot rolling process is energy intensive due to the high temperatures required; however, modern designs mitigate this with efficient heating systems, recuperative heat exchangers, and optimized firing cycles.
Strategies to improve energy efficiency include:
- Utilization of advanced refractory materials in reheating furnaces to reduce thermal losses.
- Implementation of waste heat recovery systems that convert residual thermal energy into electrical power.
- Deployment of smart automation systems to precisely control temperature gradients along the rolling mill.
Such innovations not only reduce operational costs but also significantly contribute to lowering the overall carbon footprint of the production process. This sustainable development approach is a major selling point for modern steel hot rolling mill equipment vendors and is frequently highlighted on industry resource sites.
Quality Assurance and Process Control
Ensuring product quality through precise process control is essential in hot rolling operations. Steel hot rolling mill equipment must consistently meet dimensional tolerances, surface finish requirements, and mechanical property criteria. Factors such as roll alignment, temperature uniformity, and rolling speed directly impact the quality of the final product.
Companies leading in quality assurance invest in high-end sensors, machine vision systems, and automated feedback loops that continuously monitor product dimensions and material properties. This technology allows operators to make real-time adjustments to rolling parameters, pre-empting potential deviations from set standards. Furthermore, such systems incorporate robust safety features to detect early signs of mechanical wear or misalignment, thereby minimizing downtime and reducing maintenance costs.
Research indicates that integration of a digital twin— a virtual model that mirrors the physical rolling process—can further enhance predictive maintenance protocols. This approach provides significant insights into the process parameters and facilitates a more proactive maintenance schedule, ensuring consistent performance of the steel hot rolling mill equipment.
Comparative Analysis with Cold Rolling Equipment
It is important to compare hot rolling with its cold rolling counterpart. While both processes share similarities in reducing the thickness of steel, they differ significantly in terms of process temperatures, mechanical properties, and application areas. Cold rolling is performed at or near room temperature, resulting in higher strength, improved surface finish, and tighter dimensional tolerances. However, steel hot rolling mill equipment offers advantages such as lower production costs, greater deformation capabilities, and a reduced risk of work hardening, making it more suitable for primary forming operations and mass production.
By nature, hot rolling accommodates larger deformations in a single pass and is less susceptible to issues like scale formation. In contrast, cold rolling requires additional annealing processes and extra processing steps to relieve internal stresses.
Economic and Market Perspectives
Economic factors such as the demand for high-strength, lightweight materials and the global emphasis on energy efficiency drive ongoing developments in steel hot rolling mill equipment. The industry has seen continuous investments in research and development, partly spurred by market leaders whose content on platforms like Hanrm and Hanmetallurgy highlights enhanced performance features and improved return on investment through energy savings and extended operational lifetimes.
The global steel market’s dynamic nature compels manufacturers to innovate continuously. Rising labor costs, increasing environmental regulations, and the need for superior product performance push vendors to adopt more intelligent systems and advanced manufacturing techniques. As a response, the industry witnesses not only gradual improvements in technology but also significant leaps in process control and energy management, making modern rolling mills more competitive.
Market trends indicate that the future of steel hot rolling mill equipment will likely involve increased digitalization, tighter integration of supply chain management, and enhanced predictive maintenance technologies. Clients expect comprehensive turnkey solutions, integrating state-of-the-art automation with robust engineering capabilities to ensure seamlessly consistent product quality.
Case Studies and Industry Applications
Case studies from leading steel mills demonstrate the benefits derived from upgrading to modern steel hot rolling mill equipment. For instance, a large-scale steel mill integrated advanced digital control systems into its rolling operations, leading to a 20% increase in production efficiency and a significant reduction in energy usage. Such results have been highlighted in several industrial reviews and case reports published by industry experts and reflected in marketing materials on websites like Hanrm and Hanmetallurgy.
These case studies underscore innovative approaches such as:
- Implementation of intelligent roll gap control to reduce material waste.
- Utilization of adaptive sensor networks for real-time process monitoring.
- Enhanced predictive maintenance protocols that extend equipment lifespan.
With improved process monitoring and data analysis, mills not only achieve uniform quality but also realize a shorter downtime during scheduled maintenance. The continuous feedback loop provided by modern automation systems is integral to maintaining high throughput and operational consistency.
Maintenance and Operational Best Practices
Optimal performance of steel hot rolling mill equipment is highly dependent on regular maintenance and adherence to operational best practices. Routine inspections, timely component replacements, and precise calibration of control systems are essential in keeping the equipment performing at its peak.
Some key maintenance practices include:
- Regular monitoring of roll wear and tear, ensuring that roll surfaces are maintained within specified tolerances.
- Scheduled calibration of temperature sensors and control systems for accurate readings throughout the process.
- Frequent inspections of lubrication systems to prevent friction-related issues in high-load scenarios.
- Utilization of on-line diagnostic tools to detect early signs of potential failures.
Adhering to these practices not only extends the life of the steel hot rolling mill equipment but also mitigates the risk of unexpected breakdowns that could interrupt production cycles. A well-documented maintenance strategy is crucial in minimizing downtime and ensuring that production targets are met consistently.
Future Trends in Rolling Mill Technology
The future of steel hot rolling mill equipment appears promising with trends leaning towards increased digital integration, energy optimization, and sustainable practices. Future systems are expected to incorporate even more advanced sensor technologies to monitor every aspect of the rolling process, from thermal dynamics to mechanical strains on the mill structure.
Emerging trends include:
- Digital Twins: Creating comprehensive virtual models of the mill apparatus that allow for simulations and predictive fault detection in real-time.
- Industry 4.0 Integration: Fully connected systems that can communicate seamlessly with suppliers, logistics, and end-user systems for a holistic manufacturing ecosystem.
- Advanced Material Handling: Automation systems that can efficiently handle raw materials from the furnace to the rolling mill, reducing manual intervention and process downtime.
- Enhanced Environmental Monitoring: Implementation of systems to monitor emissions, optimize fuel usage, and contribute towards a greener production environment.
Innovation in this field is driven in part by collaboration between equipment manufacturers and end-users. For example, feedback from production engineers using steel hot rolling mill equipment informs future upgrades and refinements. This collaborative approach is central to the evolution of rolling mill technology and is frequently showcased in industry exhibitions and publications.
Comparative Performance Analysis with Industry Benchmarks
When evaluating the performance of steel hot rolling mill equipment, it is essential to compare the equipment against industry benchmarks. Benchmarks typically refer to production capacity, energy efficiency, operational reliability, and product quality. For instance, mills employing newer equipment have reported up to a 15% reduction in energy use per ton of steel processed compared to older models.
Several performance indicators include:
- Roll gap sensitivity
- Thermal consistency across the billet
- Reduction in scrap rates
- Improved yield percentages
- Enhanced production throughput
These metrics are essential when designing and purchasing steel hot rolling mill equipment, as they directly affect profitability and competitive positioning in the market. The emphasis on performance analysis ensures continuous improvement in process design and operational control.
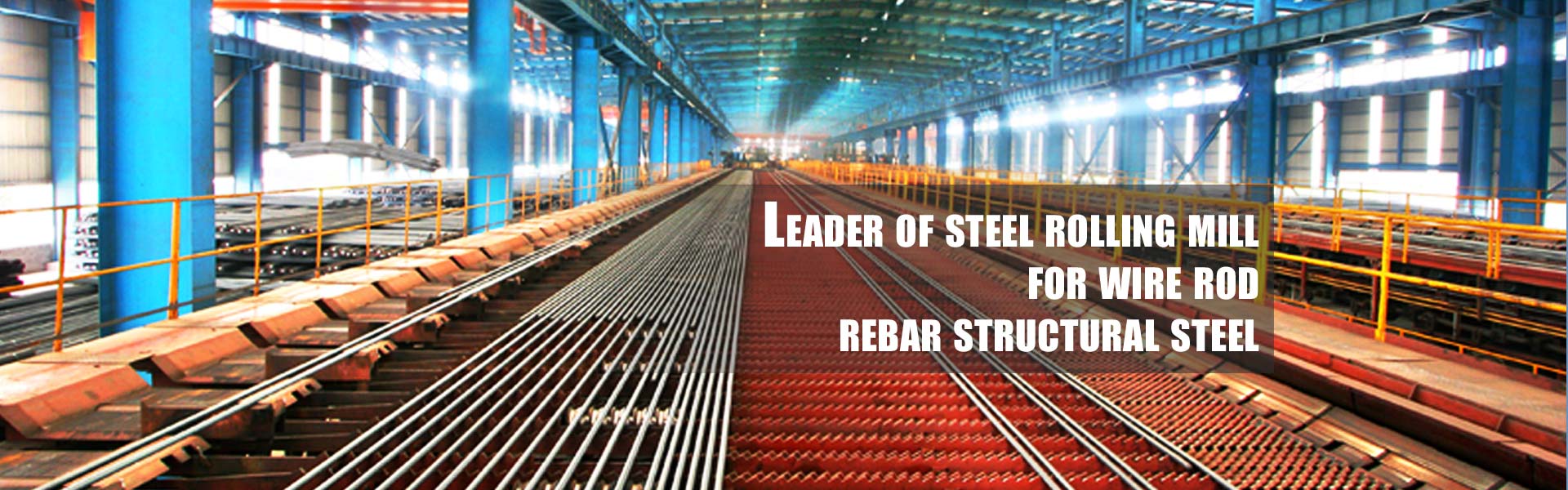
Conclusion
The comprehensive examination of steel hot rolling mill equipment outlined in this article provides valuable insights into its technical parameters, process automation, and future innovation trends. With detailed tables and descriptive analysis, professionals in the steel manufacturing industry can leverage this information to optimize production, reduce energy consumption, and maintain high quality standards in their operations.
As demonstrated, the integration of advanced control systems, real-time monitoring, and predictive maintenance are reshaping the landscape of steel rolling. Industry leaders, as highlighted on platforms like Hanrm and Hanmetallurgy, continue to drive these innovations forward. The evolution of such equipment not only supports more efficient production but also aligns with global sustainability goals.
To sum up, the robust design, extensive parameter optimization, and future-enhancing trends make modern steel hot rolling mill equipment a critical enabler in ensuring that the steel industry meets the challenges of tomorrow. Its innovations in energy efficiency, safety, and process flexibility provide a competitive edge, promising a continuously improving production environment for steel mills worldwide.
This article has provided both an academic overview and practical insights, ensuring that professionals gain a clearer understanding of the complexities involved in rolling mill operations. The detailed table of parameters, coupled with discussions on operational best practices and emerging trends, offers a valuable resource for engineers, managers, and decision-makers engaged in the modern steel production process.
In conclusion, future advancements in steel hot rolling mill equipment will undoubtedly continue to push the boundaries of efficiency, quality, and innovation. The integration of digital technologies and enhanced safety features will propel the industry into a new era of smart manufacturing, ensuring that the production of high-quality steel remains both economically viable and environmentally responsible.
NOTE
If you want to know more about the knowledge related to electric arc furnaces in the steel rolling industry and other aspects, please follow HANI’s YouTube channel for more information.
https://www.youtube.com/channel/UCQ5eAP3i7BddUh6VEQAePGA