Electric arc furnace steelmaking mainly uses arc heat, and the temperature in the arc action zone is as high as 4000 °C. The smelting process is generally divided into a melting period, an oxidation period and a reduction period. In the furnace, not only an oxidizing atmosphere but also a reducing atmosphere can be caused, so the efficiency of dephosphorization and desulfurization is high.
The iron-containing raw materials used are mainly scrap steel, accounting for more than 70%. In addition, molten iron, pig iron, direct reduced iron, hot compact, etc. can be added. Smelting takes a long time, usually at least twice the time of converter smelting. The electric arc furnace has high melting temperature and easy to control and adjust. The arc furnace arc temperature is as high as 3000-6000 °C, and the furnace temperature is up to 2000 °C. It is much higher than the temperature required for smelting general steel. It can be used for smelting alloy steel and stainless steel that cannot be smelted by converter.
The atmosphere in the electric arc furnace is easy to control and adjust. In the different stages of smelting, the furnace can not only cause an oxidizing atmosphere, but also cause a reducing atmosphere. The former is beneficial to decarburization and dephosphorization, while the latter is beneficial to deoxidation, desulfurization, easy oxidation of alloys, recovery of metal elements and Control the composition of the molten steel. The electric arc furnace equipment is relatively simple, with less investment, quick construction, small land occupation, and easy control of pollution.
However, since the required energy is provided by the high temperature generated by the electrode during the short circuit, the power consumption is large, and the electric energy consumed by smelting 1 ton of steel is about 350-600 kwh; the hydrogen and nitrogen content in the finished steel is high. Because under the action of the arc, the water vapor in the furnace is largely dissociated, and the generated hydrogen and nitrogen, such as entering the molten steel, will affect the quality of the steel. The arc is a “point” heat source, and the temperature distribution in the furnace is not uniform. When the molten pool is calm, the temperature of each part of the molten steel differs greatly. The presence of carbonaceous electrodes can increase the carbon concentration of the molten steel, which makes it difficult to smelt low carbon steel.
Scrap steel is a kind of energy-carrying resource, which can save a lot of energy by scrap steel. In large steel conglomerates, from mining, beneficiation, sintering, coking, iron making to steelmaking, steel rolling, energy consumption and pollution emissions are mainly concentrated before the steelmaking process. Studies have shown that direct steelmaking with scrap steel can save energy by 60% and save water by 40% compared with steel after iron ore.
Scrap steel is also an environmentally-friendly resource. Compared with electric arc furnace steelmaking after refining with ore, it can reduce 86% of waste gas, 76% of wastewater and 97% of waste residue, which is conducive to clean production and waste reduction.
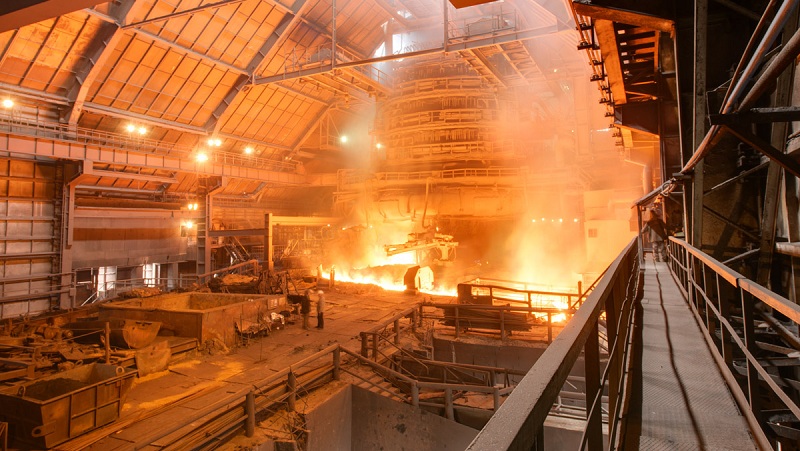