In the process of rolling profiles in the rolling mill, there are usually two processes, roughing rolling and finishing rolling. One is continuous rolling, the other is a combined rolling method with another non-continuous rolling, which is often used in alloy steel rolling or the transformation of old equipment.
Among them, there are two forms of the semi-continuous rolling method for profiles, one is shuttle rolling or looper rolling for roughing rolling and continuous rolling for finishing rolling, the other is shuttle rolling for horizontal rolling mill and continuous rollings for finishing rolling mill.
At present, the rolling method of duplex mill used in some small workshops belongs to a special semi-continuous rolling method. It is a continuous rolling method between the front and back stands. When the looper rolling finishing process between two adjacent groups of rolling mills is continuous rolling, the rolling speed is not limited and the output is high, but the rolling mill is adjusted. It is complex, difficult to change product variety and inflexible to produce. It is suitable for batch production of a few varieties of simple section profiles.
The finishing rolling process is shuttle rolling or looper rolling in the tandem mill. It is convenient to change the rolling products, but the rolling speed is low and the output is low. It is suitable for the rolling of profiles with special sections and the production of many varieties and small batches. The equipment has the advantages of compact layout, convenient adjustment, multi-wire rolling, and high output.
In addition to continuous and semi-continuous rolling, the rolling mill can also be produced by slit rolling process. Under the same conditions, the heating temperature of the billet can be reduced by about 40 C, the fuel consumption can be reduced by 20%, the electricity consumption can be reduced by 15%, and the total production cost can be reduced by 10-15%. This proves that slitting rolling is an easy and effective measure to reduce production cost.
Compared with conventional rolling, the product precision of slit rolling can be improved by 5%-6%, because the two lines bite in at the same time after slitting, the cross-section changes little, and the temperature difference between head and tail is small and the load is even. In addition, slitting rolling is only carried out on the last three stands, and the rest are micro-tension and tension-free rolling.
When the rolling mill produces the same size products with the same size billet, only 1/2 of the cross-section needs to be rolled, so the rolling pass can be reduced. At the same time, double or multi-wire rolling can be realized, which greatly improves the output of the rolling mill, which is particularly important in the production of small-sized products.
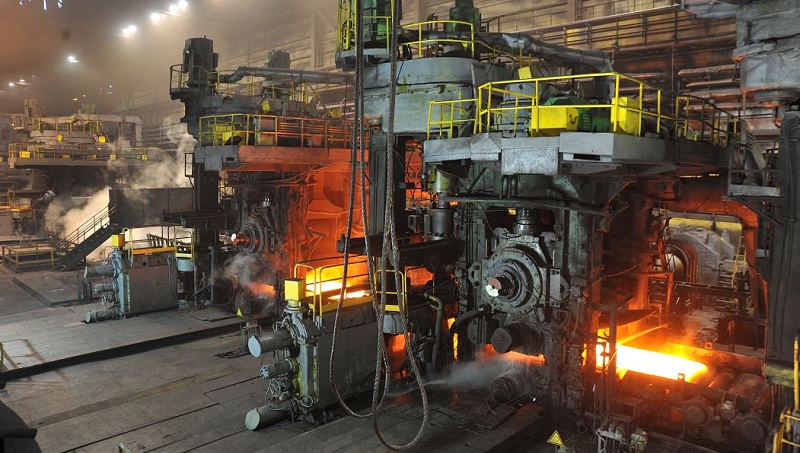