The Latest Technology of Energy Saving and Emission Reduction in Steelmaking Production
Steel is a high energy consumption industry, and energy conservation and emission reduction have been paid attention by the industry. The latest technologies for energy saving and emission reduction in steelmaking production are as follows:
1. Multifunctional Hot Metal Ladle
For example, “one package to the end” and “interface technology”, these processes can reduce the temperature of molten iron by 30-50 ℃ compared with torpedo tank, that is, it can realize the desulfurization of molten iron under high temperature and high activity state, and can realize the accurate control of iron water quantity, which is very conducive to energy conservation and emission reduction.
2. Negative Energy Steelmaking
The recovery of furnace gas and steam in steelmaking plants has been paid attention to. Some excellent converters can recover gas at a high level of more than 100m3/t and steam more than 80kg / T. In addition, dry dust removal equipment and technology of converter is being developed and applied, which can be widely spread in China and can greatly save energy and reduce emissions.
3. Energy Saving of Electric Furnace
In the aspect of electric furnace, one is the research and development and popularization of reasonable power supply system technology; the other is the cluster oxygen gun technology in improving the oxygen supply intensity and oxygen utilization efficiency; the third is the recovery of the residual heat of gasification cooling of the furnace hood for VD steam or power generation technology, so as to reduce the energy consumption of the electric furnace production and improve the production efficiency of the electric furnace.
4. Hot charging and heat transfer technology
At present, the hot charging technology of continuous casting billet has been from simply using the physical heat of the billet to realize the goal of energy-saving and cost reduction to forming the high-efficiency continuous casting of flawless continuous casting billet – the heat transfer of each steel type and reasonable hot charging temperature > optimizing the heating system and the system technology of the rolling industry. At present, the hot charging ratio of continuous casting slabs in some enterprises has exceeded 65%, and the temperature of direct loading is higher than 700 ℃. Hot delivery and hot charging of continuous casting billet is an integrated technology with high technology content and great potential for energy saving.
5. Steel Slag
The steel slag mainly focuses on the recovery of the total amount of steel remaining and ensure that the flow away from w (CAO) is less than 2% so that the steel slag can be safely and stably used; at present, it focuses on the technology and equipment research and development of the residual heat recovery and utilization of steel slag fine powder.
6. Others
The main factors are to reduce the temperature loss of the whole steel plant process (including reducing the number of ladles, accelerating the ladle turnover speed, ladle insulation, reducing the temperature of steel tapping), recycling and recycling of zinc and titanium, CO2 reduction and utilization technology research and application in the production of the steel plant.
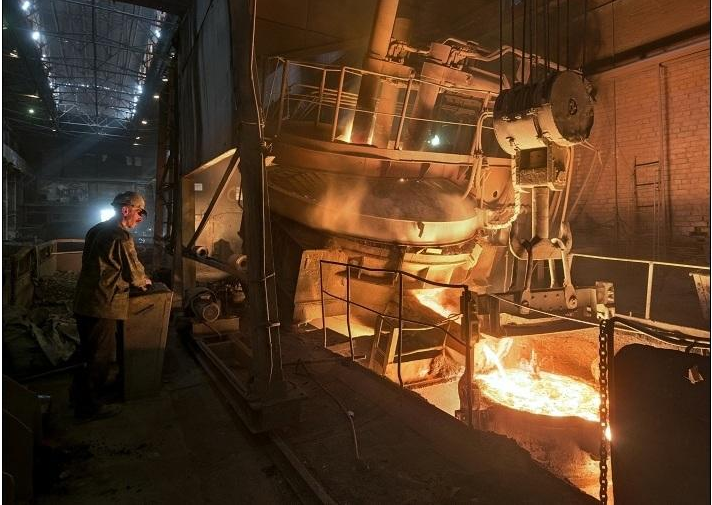