Reasons for Mill Roll Cracks
Owing to the high wear resistance and minimal plastic deformation of the cold mill roll, it is required that the surface of the cold mill roll have higher hardness and thicker hardening layer. The material of cold roll is 9Cr2Mo. The surface hardness of HS96 is obtained by surface quenching and tempering. The surface of the roll is very hard and brittle. At the same time, it has poor thermal stability and high cracking sensitivity. The thermal impact strength, tensile strength and contact fatigue strength of rolls directly affect the quality of rolls. In the process of roll use, when there are accidents such as band breakage and foreign body entry, the surface of rolls will be hit by thermal shock, and this kind of salary cannot be completely avoided at present, so the thermal impact resistance becomes the most important of cold rolling. One of the characteristics.
Strip breakage or roll sticking is due to a large amount of accumulation of steel strips between work rolls, which will cause local pressure on the rolls, leading to weld between strip and roll surface. This will make the roll surface undergo thermal shock, and the degree of roll damage depends on the severity of the accident. The factors that cause cracks depend on the performance and cause of the roll. Use conditions. Cracks caused by defects in the roll itself occur in the inside of the roll, while cracks occur in the surface and subsurface layers due to improper operation.
Reasons for Mill Roll Peeling
Owing to the limited working conditions of cold mill rolls, high surface hardness, good thermal shock resistance, spalling resistance and wear resistance are the main criteria for selecting cold mill rolls. In China, high hardness cold rolls generally use chromium-based high-carbon forged steel materials, such as 9Cr, Mo, 9cr, MoV.9Cr, W, etc. Chromium alloy high-carbon steel occurs during quenching. When transformation from alloy austenite to alloy martensite, because martensite is larger, the volume of hardened part increases. The roll surface is affected by the inner pulling force and under the control of compressive stress. After surface quenching, martensite has formed on the surface and the volume expands. However, there is no such change in the inner core, so the surface layer has an effect on the roll body. One is the tension that enlarges the volume, and the other is the tension in the weak area of metal strength. Cracks are easy to occur. With the development and extension of these cracks, the roll surface will flake off, or even break.
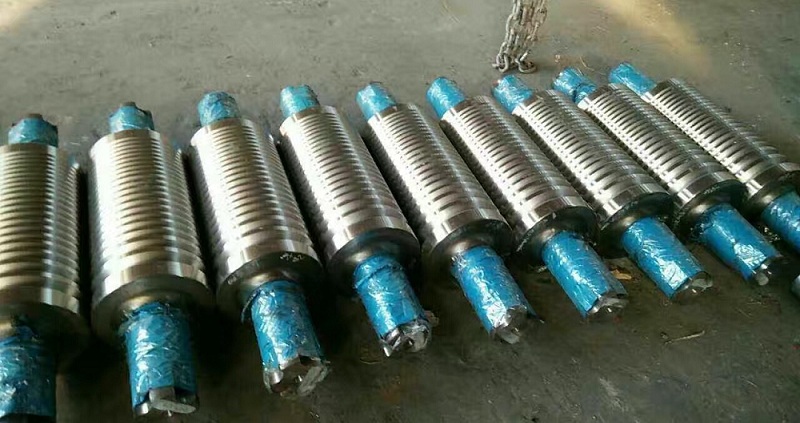