The rolling process of the rolling mill is divided into two steps: hot rolling and cold rolling.
1. Hot rolling process: the billets from the steel plant are only semi-finished products, which can only be qualified after being rolled in the rolling mill.
The continuous casting billets sent from the steelmaking plant first enter the heating furnace, and then enter the finishing mill after repeated rolling by the blooming mill. Rolling steel belongs to metal pressure processing. Rolling steel plate is like pressing dough. After many times of pressing and pushing by the rolling pin, the dough will be rolled thinner and thinner. In the hot rolling production line, the billets are softened by heating, sent to the rolling mill by the roller table, and finally rolled to the size required by the user. Steel rolling is a continuous and uninterrupted operation. The steel belt runs fast on the roller table, and the equipment is highly automated and efficient. Ingots from an open hearth can also be steel plates.
It can be sent to the hot rolling line for rolling after heating and blooming. Generally, the thickness of the continuous casting slab is 150-250mm. It is first dephosphorized to the primary rolling and then enters the finishing rolling mill through the roller table. The finishing rolling mill is composed of seven 4-high rolling mills. The front of the mill is equipped with a speed measuring roller and flying shear to cut off the plate head. Hot rolled products are divided into coil and ingot plates. After hot rolling, the plate thickness is usually a few millimeters. If the user requires a thinner steel plate, it needs to be cold rolled.
2. Cold rolling process: compared with hot rolling, the processing lines of cold rolling plants are relatively scattered. Cold rolling products mainly include common cold rolling plates, coated plates, namely tin plates, galvanized plate,s and color coated plates.
The coil sent by the hot rolling mill shall be treated three times continuously, and the oxide film shall be removed with hydrochloric acid before it is sent to the cold rolling mill. In the cold rolling mill, the uncoiler opens the coil, and then introduces the steel strip into the five stands continuous rolling mill to form the thin coil. There are also different specifications of ordinary steel coils coming out of the five racks. They are processed according to various requirements of users, so as to produce various products of different quality.
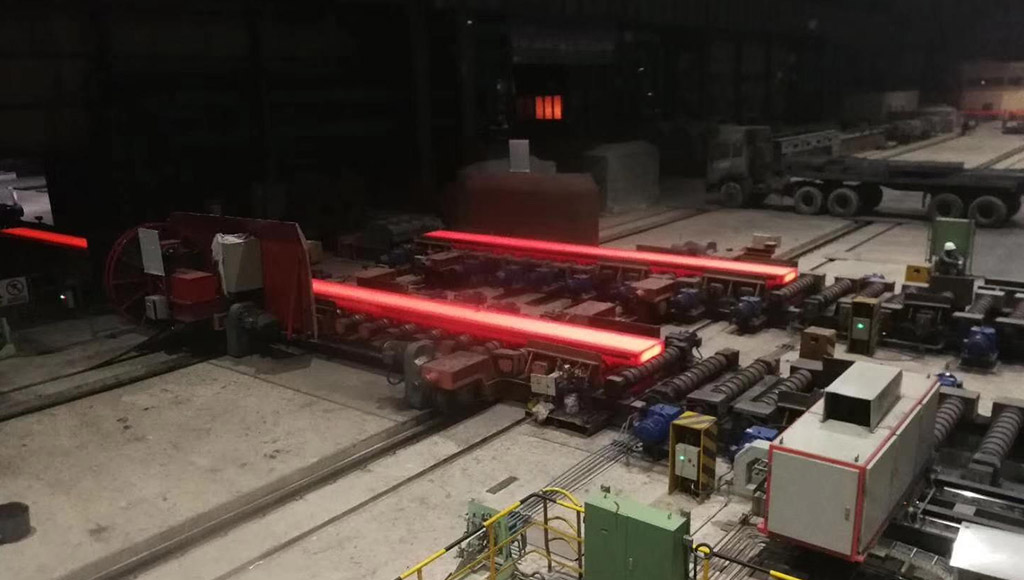
Rolling process
Generally, the rolling process of a single stand 20 high cold rolling mill can be divided into three stages: feeding, threading, reversible rolling, unloading, and rewinding. 20 high rolling mill, especially Sendzimir 20 high rolling mill, uses high tension for rolling; the rolling process starts after the coiler / uncoiler before and after the rolling mill applies tension, which is the feeding and threading stage.
Feeding and threading stage: generally, the feeding trolley is used to send the steel coil to the uncoiler drum; the floating uncoiler is often used for uncoiling to ensure that the steel strip is always in the central position of the rolling mill; the floating uncoiler is controlled by the general hydraulic cylinder of the photoelectric centering device; after uncoiling, the steel strip is straightened by the straightening machine (three roll straightening head or five roll straightening machine); some rolling mills are equipped with hydraulic shears for cutting Head: the steel strip is directly sent to the 20 high rolling mill by using the tilting guide board to cross the front coiler of the machine; then the uncoiler continues to send the steel strip forward through the rolling mill until it is sent to the jaw of the coiler behind the machine. The jaw holds the steel strip head and wraps it on the drum for 2-3 turns, then stops the belt feeding and passes through the belt tie.
Reversible rolling stage: after wearing the belt, first place the upper and lower work rolls (the work rolls have been removed), then adjust the rolling line, close the rolling mill closed doors, press the front press plate down, the outlet side wipes press the steel strip, the rolling mill process lubrication cooling system starts the liquid supply, the rolling strip steel presses down, the coiler turns to the front tension of the steel belt, the machine thickness gauge and the speedometer enter the rolling line, the unit is running and the first rolling is started.