One - Stop Majordomo For Steel Plants
We mainly provide design, manufacturing, installation and after-sales service for various steel production lines such as wire rod, bar, steel bar, angle steel, pipe, etc.
We provide various rolling mills, including small rolling mills, large rolling mills, rough rolling mills, medium rolling mills, etc., as well as finishing mills, which can improve your production capacity and save costs.
We also have all the auxiliary equipment required for hot rolling mills, including 1# shear, 2# shear, 3# shear, double length shear, water washing scale equipment, speed increaser, speed reducer, cylinder system, hydraulic system, etc.
We can also quickly provide spare parts required for rolling mills, such as rollers, bearings, sleeves, guides, universal joint couplings, etc. to meet customer requirements.
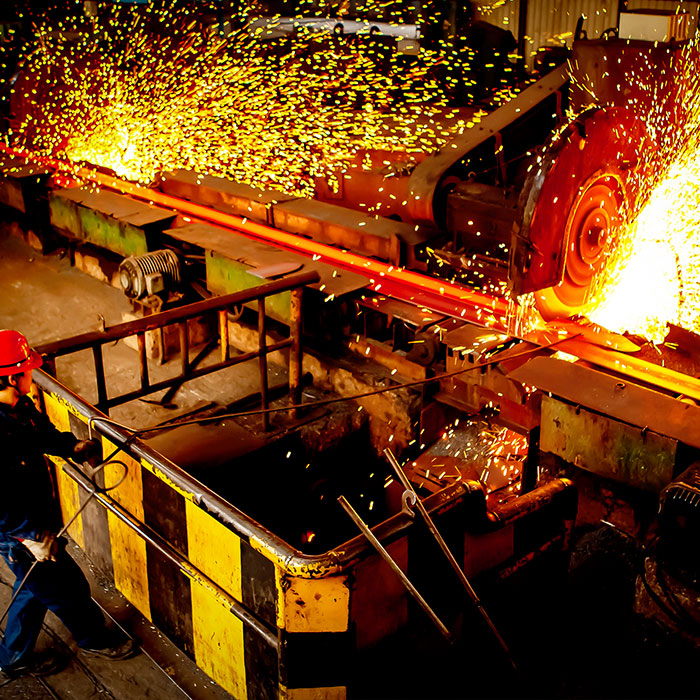
One-Stop Construction And Procurement Platform For Steel Mills
- Production Line
- Rolling mill
- Auxiliary equipment
- Spare parts
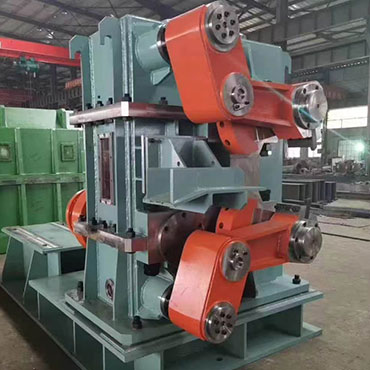
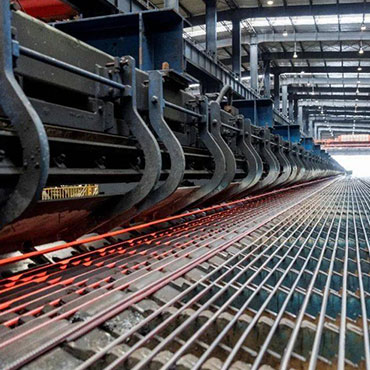
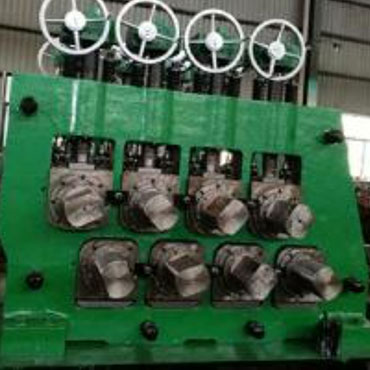
What Can Our Equipment Do?
We can provide design and equipment manufacturing of various steel product rolling production lines, including bar rolling mills, wire rolling mills, rebar rolling mills, steel bar rolling mills, plate rolling mills, coil rolling mills, strip steel rolling mills, profiles (angle steel, square steel, I-beam, C-beam, channel steel, etc.), spring steel, various carbon steels, etc.










Project Cases
We attach great importance to every customer and have very successful cases all over the world (including steel rolling mills under construction and completed), which have given us very deep accumulation in the steel industry, so that we can better achieve our customers’ goals.
Professional Metallurgical Equipment Manufacturer.
Hani Steel specializes in the production of various steel rolling metallurgical equipment, integrating R&D, design, manufacturing and sales.


Design Engineer
Frequently Asked Questions
In order to better meet customer needs, the issues that customers care about are also our concerns.
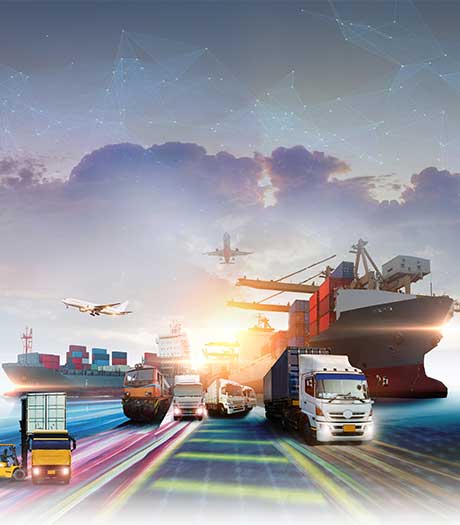
Don’t worry. When the equipment arrives at the customer’s factory,
our engineers will assist with installation, commissioning and training until the workers can operate it themselves.
We are responsible for container loading and wire fixing. In case of damage, we will send you spare parts.
Our plant has a history of about 25 years in the field of steel rolling equipment service, total solutions for steelmaking and product components.
And our equipment has been exported to East Asia, South Asia, the Middle East, Africa and other regions. There are a large number of successful cases
and good feedback.
Of course, brand licensing is possible. We accept OEM service.
If the parts are in stock, it usually takes 7-14 days. If the parts are not in stock, it will take 30-45 days, depending on the factory capacity.
If it is a customized total solution of the customer, we will negotiate with the customer for delivery time.
Our QC team adheres to TQM to ensure quality. Every step is up to standard.
At the same time, we can take clear photos and videos for you if needed.
Steel Rolling Knowledge
Here are mainly some industry information, company dynamics, product knowledge, etc.