There are many types of rolls. Commonly used rolls include cast steel rolls, cast iron rolls and forged rolls. According to the forming method, the roll can be divided into casting roll and forging roll. Casting roll refers to the roll made by direct casting molten steel or molten iron. Casting roll can be divided into cast steel roll and cast iron roll according to its material. According to the manufacturing method, the roll can be divided into integral casting roll and compound casting roll. The forged roll is made of white alloy steel and the forged roll is made of semi coil steel. According to the treatment method, it can be divided into the integral roll, metallurgical composite roll and combined roll.
Compared with the composite roll, the outer layer, core and neck of the integral roll are cast or forged from a single material. The different structures and properties of the outer layer of the roll body and the roll neck are controlled and adjusted by casting or forging process and heat treatment process. Forging roll and static casting roll are integrated roll. Integral roll is divided into integral casting roll and integral forging roll.
Metallurgical composite casting roll mainly includes semi washing composite casting, overflow (full washing) composite casting and centrifugal composite casting, as well as continuous casting and coating (CPC cladding continuous casting process), spraying, hot isostatic pressing (hip Hip), electro slag welding and other special composite methods. Composite volume is mainly mosaic composite volume. According to the manufacturing materials, the rolls can be divided into cast steel series, cast iron series and forged series.
The commonly used heat treatment types of roll are stress relief annealing, isothermal spheroidizing annealing, diffusion annealing, normalizing, tempering, quenching and low-temperature treatment.
Why does metallurgical cast steel roll need high-temperature diffusion treatment?
During the solidification process of cast steel roll, dendrite will cause intragranular segregation of alloy composition. This segregation is caused by the failure to realize the sequential curing of the roller body, inner layer and outer layer during the curing process of the roller. The larger the diameter of the roller body, the longer the length of the roller body and the larger the solidification temperature gradient, the more serious the segregation caused by alloy solidification. With the increase of alloy content in alloy cast steel roll, the segregation index during solidification increases, and the inhomogeneity of composition also increases. Therefore, in order to make the atoms of alloy elements fully diffuse and obtain a uniform austenite structure, it is necessary to heat the high alloy cast steel roll to 150 ~ 250 ℃ higher than AC3. This heat treatment method is called high-temperature diffusion treatment.
Why does alloy cast steel roll need spheroidizing annealing heat treatment?
The spheroidizing annealing heat treatment of alloy cast steel roll is mainly to improve the cutting performance of the roll, improve the cutting efficiency, and prepare the corresponding structure for subsequent quenching treatment. After spheroidizing annealing, the carbides in the microstructure change from flake to sphere, that is, the spherical or granular carbides are uniformly distributed on the ferrite matrix, forming a spherical pearlite structure. The spheroidizing temperature is usually slightly higher than AC1 critical point. If the temperature is too low, the spheroidizing time will be too long; if the temperature is too high, granular pearlite with different sizes will appear.
Why does alloy cast steel roll need quenching heat treatment?
The quenching process of alloy cast steel roll is to heat them to the critical temperature (ACM or AC1), keep them for a certain time to make them fully austenitized, and then quickly cool them to the bainite transformation zone at a higher cooling rate, exceeding the critical cooling rate, so as to obtain bainite structure in the working layer of roll body.
The main purpose of quenching and heat treatment of alloy cast steel roll is to make the working layer of the roll obtain a good suitable structure, give full play to the role of alloy elements in the roll, and improve the hardness and wear resistance of the roll.
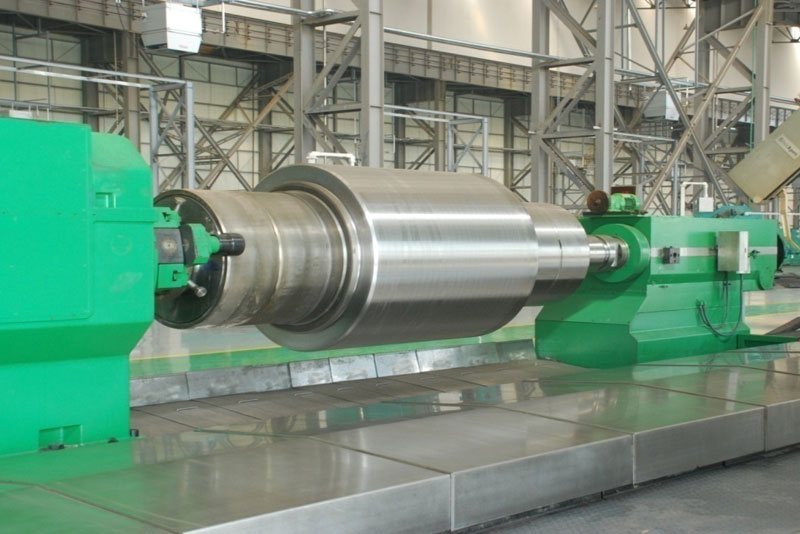