Roller Hearth Reheating furnace is a piece of the important equipment in thin slab continuous casting rolling mill production line. It plays a connecting role in function. On the one hand, it heats the slab from continuous casting to the tapping temperature required by the rolling process of 1150 (+10). This temperature precision is much higher than the temperature difference of (+30)(+30)(+10). Thus, it lays a foundation for the production of ultra-thin hot strip products. On the other hand, the roller hearth reheating furnace also plays an important buffer role in the whole process.
Summary of Roller Heating Reheating Furnace
Roller hearth reheating furnace conveys heat treatment materials by roller in the furnace. A roller is installed every certain distance along the whole length of the furnace. The material runs on the roller, and burners can be arranged on the upper and lower hearth of the roller for heating. There are two kinds of rollers, ring roll (with disc roll ring) and flat roll. The former can only be used for heating plate, section steel, pipe, and bar. The outer roll sleeve of rollers is usually made of heat-resistant steel, and some of them are made of silicon carbide. High-temperature furnaces (1000-1150 C) adopt water-cooled shaft and heat-resistant steel furnace rollers with adiabatic lining, or full water-cooled furnace rollers. In order to prevent the furnace roll from bending, the roll working at high temperature must rotate continuously. When the furnace is empty burned or not discharged, it should also swing or rotate at a low speed of 0.5-1.5 cycles per minute. Roller hearth reheating furnace is widely used in 53 processes such as normalization, annealing, quenching, and tempering because of its fast and uniform heating on both sides of the material.
The Function of Roller Heating Reheating Furnace
The thin slab from the continuous caster is heated uniformly to the rolling temperature according to the technological requirements. The input temperature of continuous casting slab in the production line is generally between 850 and 1050, the exit temperature (rolling temperature) is between 1100 and 1150, and the furnace temperature needs to be raised by 50 to 300 degrees. It is required that the temperature difference between the length and width of the slab should be less than < 10 C, and the temperature at the edge of the slab (within the range of about 40 rams) should be about 40 C higher than that at the middle of the slab.
When rolling a single-foot slab, the furnace can store a number of single-foot slabs. When the rolling mill changes rolls or stops rolling in an accident, the thin slabs sent by the continuous caster can be stored in the reheating furnace to ensure the normal production of the continuous caster, and the furnace plays a buffer storage role. According to the requirement of rolling technology, the buffer time of single-foot billet production should be more than 12 minutes to ensure that the mill has sufficient time to change rolls and deal with accidents.
In the thin slab continuous casting and rolling production line, besides the roller hearth reheating furnace, some production processes use induction heating, coil insulation furnace and shorter roller hearth furnace combination (ISP process) and walking beam reheating furnace (CONTROL process) to meet the above requirements, but due to various factors, this combination heating method has not been greatly developed. At present, the roller hearth heating furnace with longer furnace length is still the mainstream reheating equipment in thin slab continuous casting and rolling production process.
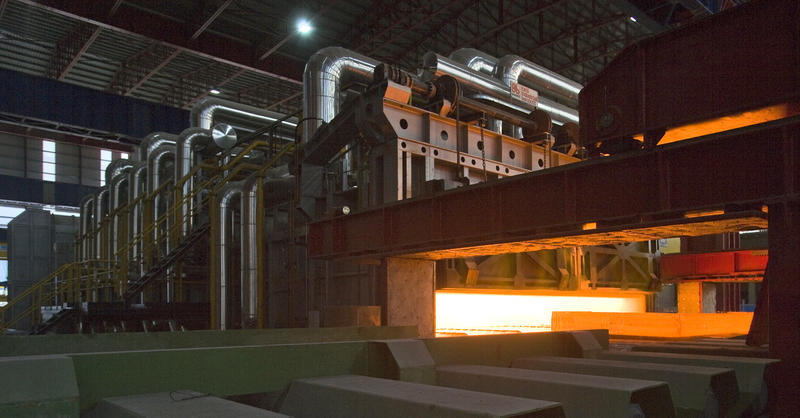