1. Definitions
Rolls are a tool to produce plastic deformation of the metal. It is an important consuming part to determine the efficiency and quality of the rolling mill. Roll is an important part of the rolling mill. The pressure generated by a pair or group of rolls is used to roll the steel. It mainly bears the influence of dynamic and static load, wear and temperature change during rolling.
2. Common Roll Materials
The commonly used materials of hot rolling roll include 55mn2, 55cr, 60CrMnMo, 60simnmo, etc. the hot rolling roll is used in the processing of billet, thick plate and section steel. It bears the influence of strong rolling force, severe wear and thermal fatigue. Moreover, the hot roll works at high temperatures and allows the diameter wear within the unit work volume. Therefore, it does not require surface hardness, but only high strength, toughness and heat resistance. The hot rolling roll is only normalized or quenched as a whole, and the surface hardness shall be hb190 ~ 270.
3. Roll Classification
There are many kinds of rolls, including cast steel roll, cast iron roll and forging roll. There are also a few cemented carbide rolls on the profile rolling mill.
Forming method: casting roll refers to the roll made by pouring molten steel or molten iron directly. Casting roll can be divided into cast steel roll and cast iron roll according to material; According to the manufacturing method, it can be divided into integral casting roll and composite casting roll. Forging rolls are divided into:(1)forging alloy steel rolls; (2) forging semi steel roll; (3) forging semi high speed steel roll; (4) forged white cast iron roll.
Process method: integral roll, metallurgical composite roll and combined roll
1. The integral roll is relative to the composite roll. The outer layer, center and neck of the integral roll are made of a single material by casting or forging. The different structures and properties of the outer layer and neck of the roll are controlled and adjusted by the casting or forging process and heat treatment process. Forged roll and static casting roll belong to integral roll. The integral roll is divided into integral casting roll and integral forging roll.
2. Metallurgical composite casting rolls mainly include semi flushing composite casting, overflow (full flushing) composite casting and centrifugal composite casting. In addition, there are also composite rolls manufactured by special composite methods such as continuous pouring process for cladding, spray deposition, hip hot isostatic pressing and electroslag fusion welding. The combined roll is mainly the insert sleeve combined roll.
3. According to the manufacturing materials: cast steel roll, cast iron roll and forging roll.
4. Common heat treatment types of rolls: stress relief annealing, isothermal spheroidizing annealing, diffusion annealing, normalizing, tempering, quenching and cryogenic treatment.
Rolls have different classification methods. According to the shape of the roll body, it is divided into cylindrical and noncylindrical. The former is mainly used for the production of plates, strips, profiles and wires, and the latter is mainly used for the production of pipes.
It is divided into work roll and backup roll according to whether it contacts the rolled piece. The roll directly contacting the rolled piece is called work roll; In order to increase the stiffness and strength of the work roll, the roll placed on the back or side of the work roll without direct contact with the rolled piece is called backup roll.
According to the frame used, it is divided into the initial roll, roughing roll, intermediate roll and finishing roll. According to the variety of rolled products, it is divided into strip roll, rail beam roll, wire roll and pipe roll. It can also be divided into hot roll and cold roll according to the state of rolled piece during rolling.
According to the hardness value:
(1) Soft roll: the shore hardness is about 30 ~ 40, which is used for roughing mill of billet opener and large section steel mill.
(2) Semi-hard roll: the shore hardness is about 40 ~ 60. It is used for roughing mill of large, medium and small section steel mill and steel plate mill.
(3) Hard surface roll: the shore hardness is about 60 ~ 85. It is used for roughing mill of thin plate, medium plate, medium section steel and small section steel mill and support roll of four high mills.
(4) Extra hard roll: the shore hardness is about 85 ~ 100, which is used for cold rolling mill.
Rolling mill type: according to the rolling mill type, the rolls can be divided into the following three categories:
(1) Plane roll: that is, the roll of plate and strip rolling mill, and its roll body is cylindrical. Generally, the roll of hot-rolled steel plate mill is made into micro concave shape, and a better shape can be obtained when it is heated and expanded; The roll of cold-rolled steel plate mill is made into micro convex shape. During rolling, the roll bends to obtain good shape.
(2) Grooved roll: it is used for rolling all kinds of large, medium and small section steel, wire rod and blooming. A rolling groove is engraved on the roll surface to form the rolled piece.
(3) Special roll: it is used for special rolling mills such as steel pipe rolling mill, wheel rolling mill, steel ball rolling mill and piercer. The roll of this rolling mill has various shapes. For example, the roll rolled by the cross rolling principle in steel pipe rolling has conical, waist drum or disc shape.
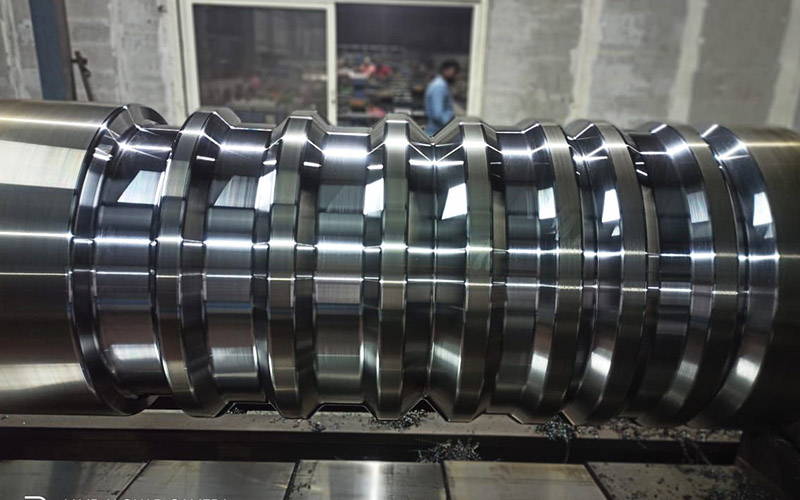
4. Working Principle
Heat crack resistance
Generally, strength and thermal crack resistance are the main requirements for roughing rolls; The working roll weight of the small 20 high mill is only about 100g, while the backup roll weight of the wide and thick plate mill has exceeded 200t. When selecting the roll, first select the main material (cast iron, cast steel or forged steel of various levels) for safe bearing according to the basic strength requirements of the rolling mill for the roll.
Hardness
The speed of the finishing roll is high, and the final rolling product must have a certain surface quality, which is mainly required by hardness and wear resistance. Then consider the wear resistance of the roll.
Impact resistance
In addition, there are some special requirements for the roll. For example, when the reduction is large, the roll is required to have strong biting ability and good impact resistance.
Finish
When rolling thin products, there are strict requirements on roll rigidity, uniformity of microstructure and performance, machining accuracy and surface finish.
Cutting performance
When rolling complex section steel, the cutting performance of the working layer of the roll body should also be considered.
When selecting rolls, some performance requirements for rolls are often opposite to each other, and the purchase and maintenance costs of rolls are very expensive. Therefore, we should fully weigh the advantages and disadvantages of technology and economy, and decide whether to use cast or forged, alloy or non alloy, single material or composite material.
5. Working conditions
When in use, it is further affected by various periodic stresses, which is determined by three factors: ① rolling mill, rolled products and rolling conditions, as well as the reasonable selection of rolls; ② Roll material and its manufacturing quality; ③ Roll use and maintenance system.
6. Roll Variety
Cast iron roll
Generally classified according to the manufacturing process: the roll with white structure (matrix + carbide) in the working layer due to the chilling effect of metal mold is called chilled cast iron roll; The roll with pitting structure (matrix + carbide + graphite) obtained by appropriately increasing the carbon equivalent of molten iron by the above method is called infinite chilled cast iron roll. The roll with coarse pitting structure can be obtained by using sand lined metal mold and continuously increasing carbon equivalent, which is called semi chilled cast iron roll. In all the above types of tissues, where the graphite is spherical, it is called nodular cast iron roll; Add the word “compound” to the roll of compound casting.
Cast steel roll
Generally classified by carbon content: hypereutectoid steel roll with extremely high carbon content (1.4 ~ 2.4%) is commonly known as semi steel roll, and high carbon semi steel roll has actually extended into the field of cast iron; Another type of high carbon hypereutectoid steel roll is graphite steel roll, whose graphite is obtained by inoculation and heat treatment.
Forged steel roll
Generally classified by use.
other
Except those with special processing technology, they are directly called by material. For example, the roll forged with electroslag remelting casting blank is called electroslag remelting forging roll.
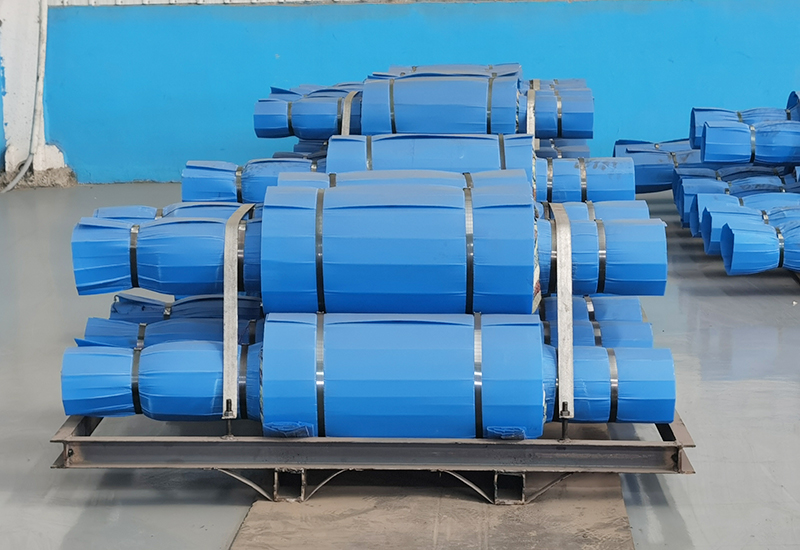
7. Cause of damage
The working conditions of rolls in rolling mill parts are the most complex. Residual stress and thermal stress will be produced in the preparation process before manufacturing and use. When in use, it is further affected by various periodic stresses, including bending, torsion, shear, contact stress and thermal stress. The distribution of these stresses along the roll body is uneven and changing. The reason is not only the design factors, but also the wear of the roll in use, the continuous change of temperature and roll shape. In addition, abnormal rolling conditions often occur. If the roller is cooled improperly after use, it will also be damaged by thermal stress. Therefore, in addition to wear, there are often cracks, fractures, spalling, indentation and other local damage and surface damage. A good roll should have a better match between its strength, wear resistance and other performance indexes. In this way, it is not only durable under normal rolling conditions, but also has less damage in some abnormal rolling conditions. Therefore, when manufacturing the roll, the metallurgical quality of the roll should be strictly controlled or supplemented by external measures to enhance the bearing capacity of the roll. Reasonable roll shape, pass, deformation system and rolling conditions can also reduce roll working load, avoid local peak stress and prolong roll life.
8. Repair Method
Bearing wear
Repair method of polymer composite material: it has comprehensive properties such as super adhesion, excellent compressive strength, wear resistance and corrosion resistance. When the wear size of the transmission part is relatively small, the polymer composite material can be disassembled and repaired on site, which can avoid mechanical processing, without the thermal influence of repair welding thermal stress, and the repair thickness is not limited, At the same time, the wear resistance of the product and the concession of metal materials ensure 100% contact and coordination of the repaired parts, reduce the impact vibration of the equipment, avoid the possibility of wear, greatly prolong the service life of equipment components (including bearings), save a lot of downtime for the enterprise and create great economic value.
Cold welding repair method: the cold welding machine uses the principle of electric spark high-frequency discharge to carry out nonthermal surfacing on the metal surface, so it does not deform, anneal, undercut and residual stress in the process of repairing roll sand holes, scratches and other defects, and does not change the metal structure state. With high repair precision and coating thickness ranging from a few microns to a few millimeters, it can deposit, seal and repair defects such as wear, scratch, pinhole, crack, defect deformation, hardness reduction, trachoma and damage on metal workpieces. It only needs grinding and polishing, and can also carry out various mechanical processing such as turning, milling, planing and grinding, as well as post-processing such as electroplating.
Fracture cause
(1) Brittle fracture, the fracture shape of this kind of roll is relatively flat, and the roll body surface around the fracture is relatively neat;
(2) Ductile fracture, the fracture shape of this kind of roll is mostly “mushroom head”, and the roll body near the fracture is crushed.
Both brittle fracture and ductile fracture are caused by the roll stress exceeding the core strength. The reason is related to the residual stress of the roll itself, the mechanical stress during rolling and the thermal stress of the roll, especially when the temperature difference between the surface and core of the roll body is large. This temperature difference may be caused by poor roll cooling, interruption of cooling or overheating of roll surface at the beginning of a new rolling cycle. The huge temperature difference between the surface and the core of the roll causes large thermal stress. When the large thermal stress, mechanical stress and residual stress of the roll exceed the core strength of the roll, the roll is broken. Compared with the roll with brittle fracture, the roll with ductile fracture has better toughness and is less prone to fracture.
There are four kinds of stress-causing roll failure:
(1) Residual stress during manufacturing;
(2) Mechanical stress during rolling;
(3) Microstructure stress of roll during rolling;
(4) Thermal stress caused by temperature difference inside and outside the roll.
If the fracture is caused by excessive manufacturing residual stress, the roll break usually occurs several times before the roll is initially used on the machine, and it is the first few rolled pieces of rolling.
If the fracture is caused by mechanical stress, a large mechanical stress is required. The most stressed part of the roll is the drive-end roll neck. If the mechanical property index of the material is insufficient, the first damage is the drive end roll neck under normal rolling conditions. From the actual rolling and roll breaking situation, the roll body fracture is not caused by mechanical stress.
The content of retained austenite in the outer layer has the greatest influence on the microstructure stress. Under the alternating action of rolling temperature, rolling pressure and water cooling, retained austenite transforms from austenite to martensite or bainite. Due to the small specific volume of austenite and the large specific volume of martensite, the volume expansion in the process of microstructure transformation will lead to greater compressive stress in the working layer of the rolling roll and greater tensile stress in the core, Once the core stress exceeds the strength of the material, it will inevitably cause roll fracture. Considering the influence of retained austenite on microstructure stress and the working conditions of hot strip mill rolls, the content of retained austenite of rolls is generally controlled to less than 5% to ensure safe use. The content of retained austenite in the outer layer of the fractured roll is less than 1%, so the structural stress can be ignored. Roll fracture may also be related to thermal stress caused by uneven temperature. During the use of the roll on the machine, due to the close contact with the rolled material, the roll surface temperature rises rapidly, while the temperature rise of the roll core is slow. At this time, the temperature difference between the roll surface and the roll core is at the maximum value, and the roll thermal stress caused by the temperature difference is also at the maximum value. If the thermal stress of the roll and the residual stress of the roll are superimposed and exceed the strength limit of the roll core, the roll fracture accident may occur.
Fracture prevention method
The prevention of fracture should be carried out from four aspects: reducing manufacturing residual stress, mechanical stress, structural stress and thermal stress.
Generally, most of the manufacturing residual stress will be eliminated during heat treatment and will be gradually eliminated with the extension of the storage time of the roll. Therefore, the risk of roll breakage can be reduced by storing the new roll for a period of time. The main way to avoid large mechanical stress is to avoid undercooling steel. The method to reduce the microstructure stress is to control the content of residual austenite in the working layer of the roll body below 5% by heat treatment. The way to reduce thermal stress is to cool the roll well during steel rolling. Manufacturing residual stress, mechanical stress, structural stress and thermal stress are the main causes of high chromium steel roll fracture. Good heat treatment, rolling conditions and cooling can effectively prevent high chromium steel roll fracture.
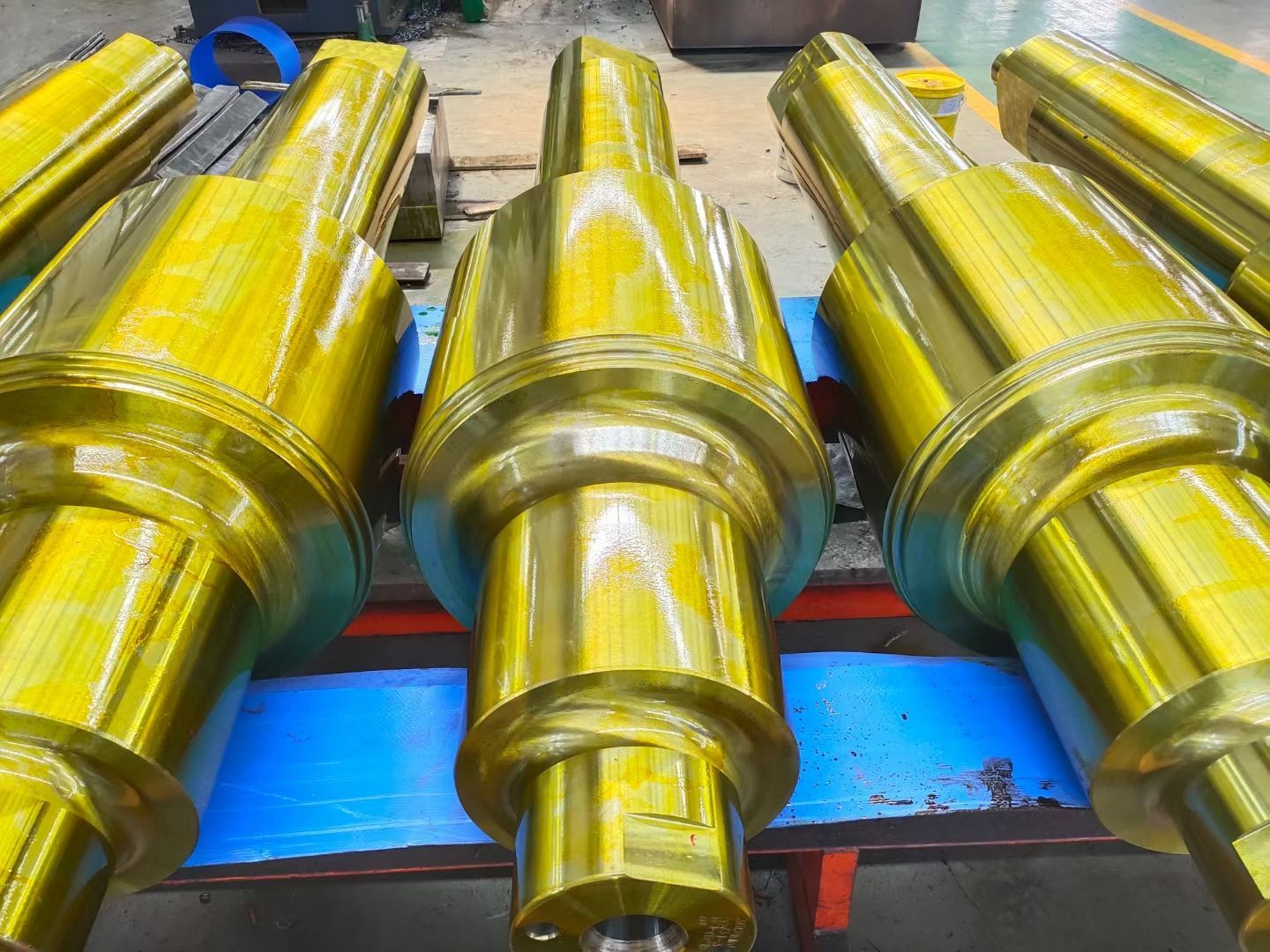