What is the Main Equipment of Short-process Electric Furnace Steelmaking and Continuous Casting?
The “short process” of steelmaking specifically refers to a compact production process that combines electric arc furnace and continuous casting-rolling, which is mainly manifested in a compact process formed by raw material preparation-electric arc furnace smelting-refining-continuous casting-rolling. The electric arc furnace short process has become one of the two main processes in the world’s steel production due to its advantages in investment, efficiency, and environmental protection.
This article will introduce in detail the main equipment details of electric furnace steelmaking and continuous casting.
1. Supporting Device for Ladle
During continuous casting, molten steel is generally supplied to the continuous caster with a ladle. The equipment that transports the ladle to the top of the intermediate tank and supports it is called the ladle support equipment.
At present, there are four types of ladle supporting equipment: crane hanging type, ladle support type, ladle car type, and ladle turret type.
(1) Crane hoisting bag type: The ladle is hoisted to the specified position by a crane. Has been rarely used.
(2) Ladle support type: support the ladle with support at a specified position. This method is used to achieve continuous furnace pouring, so it is rarely used.
(3) Ladle cart type: The ladle cart is a walking trolley that can support two ladles and straddle the intermediate tank. This device, the continuous casting machine and the crane for lifting the ladle must be in the same span of the workshop, and in order to ensure continuous furnace pouring, a continuous casting machine must also be equipped with two ladle wagons. The narrow pouring platform of this support device restricts the installation of various other machinery, and because it is concentrated with the continuous casting machine, it interferes greatly with each other and affects the operation.
(4) Ladle turret type: The ladle turret consists of a fixed part and a rotating part. The fixed part is fixed on the foundation with bolts, and the rotating part and the fixed part are combined with the bearing of the rotating cup. In addition, the rotating arm of the turret can be rotated 180°, and can be raised and lowered, and the two ends can also sit on the ladle and install the metering device at the same time. This kind of device has a relatively simple structure, is easy to operate remotely, and is safe, reliable and efficient. It is currently the main equipment used.
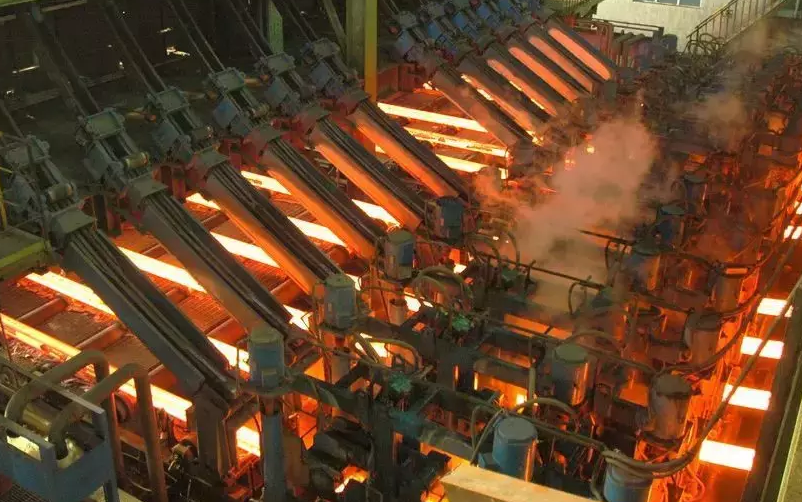
2. Intermediate Tank
The function of the intermediate tank is mainly to receive the molten steel flowing out of the ladle and distribute the molten steel to the various molds. Therefore, it can not only control the flow rate of molten steel injected into the mold and uniform the temperature of the molten steel, but also creates conditions for the floating of non-metallic inclusions in the steel. That is, when the height of the steel liquid level in the tank is kept constant, it also has the effect of stabilizing.
3. Tundish Truck
The main function is to drag the tundish. Generally, it has three functions of walking, lifting, and fine adjustment of the nozzle position. Even if it is required to quickly exchange the tundish for continuous furnace pouring, it can meet the operational requirements.
There are two driving methods for tundish trucks: electric and hydraulic. Small-capacity tundishes are electrically driven, while large-capacity tundishes are mostly hydraulic. In addition, a load cell can be equipped on the track of the tundish car to measure the weight of the molten steel.
4. Crystallizer
The important function of the mold is to cool and solidify the molten steel into a steel billet shell of a certain thickness to prevent the billet from breaking when it is pulled out of the mold. Molds generally require the use of pure copper or copper alloy materials with good thermal conductivity and small thermal deformation, internal slotting or drilling, so that high-pressure cooling water can flow through at a flow rate of 5-10m/s. In order to improve the wear resistance of the mold wall, measures such as chrome plating are generally taken on the inner surface. The structure of the crystallizer can be roughly divided into three types: integral type, tube type and assembly type.
5. Mould Vibration Device
The mold vibration device can make the mold reciprocate, mainly to prevent the molten steel from sticking to the mold, so as to prevent the solidified shell from being broken and causing a steel breakout accident, and at the same time, it can improve the heat conduction in the mold and the quality of the billet. It is also possible to input lubricant into the crystallizer.
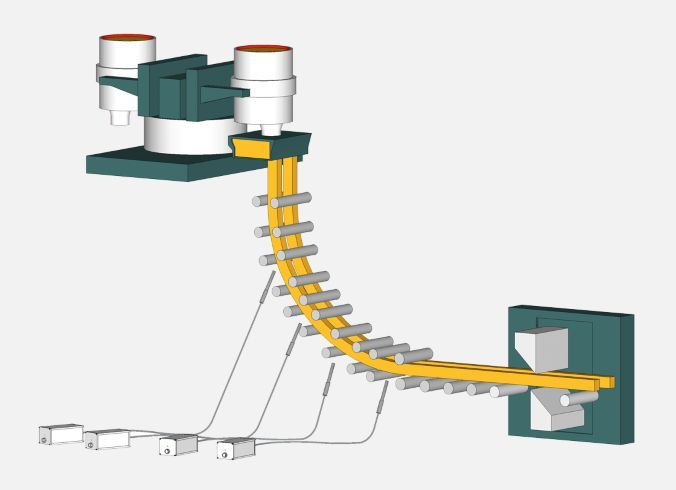
6. Secondary Cooling System
The solidified shell of the billet coming out of the mold is very thin, about 10-30mm thick, and the inside is still molten steel. If there are defects on the surface of the billet, molten steel may flow out. Therefore, in order to solidify the billet from the mold as completely as possible, cooling must be continued, which is called secondary cooling.
7. Drawing and Straightening
The billet straightening device is also called the billet straightening roll. Its main function is to continuously pull the billet out of the mold at an adjustable speed, and it can also straighten the bent billet on the arc continuous casting machine. And make it output along the horizontal direction.
8. Cutter
The function of the cutter is to cut the continuously poured steel billet into finished products according to a fixed length. There are two commonly used cutters.
(1) Flame cutting. The gas used in flame cutting is mainly acetylene or propane with high-pressure oxygen for combustion, and some use coke oven gas-oxygen cutting. Advanced flame cutters should include the walking device, cutting gun device, end face detection and billet clamping device, etc. The operation has ordinary, manual, semi-automatic and fully automatic operations. The flame cutting speed is slow, the metal loss is about 1%~2%, and the pipeline is also complicated and prone to failure and environmental pollution.
(2) Mechanical shearing. At present, the most common mechanical shear is flying shear. Although flying shears are complicated in equipment, simple in operation, reliable in use, and extremely low in metal loss, their productivity is very high.
9. Induction Bar
The function of the starter bar is to extend the starter head into the mold as a live bottom. After pouring, the molten steel and the starter head are condensed together, and at the same time, the traction force of the pull roller is transmitted to the billet, and then the billet is gradually removed from the mold. The mold is pulled out and runs along the guiding mechanism of the continuous casting machine.
The starter bar is composed of two parts: the starter head and the starter body. In order to prevent wear and deformation on the vertical continuous casting machine, some use an integral structure.
But what is used on the arc continuous caster is a unidirectional flexible chain link structure. In addition, there are dovetail slot types, tack types and hook head types, among which the dovetail slot type is more adopted.
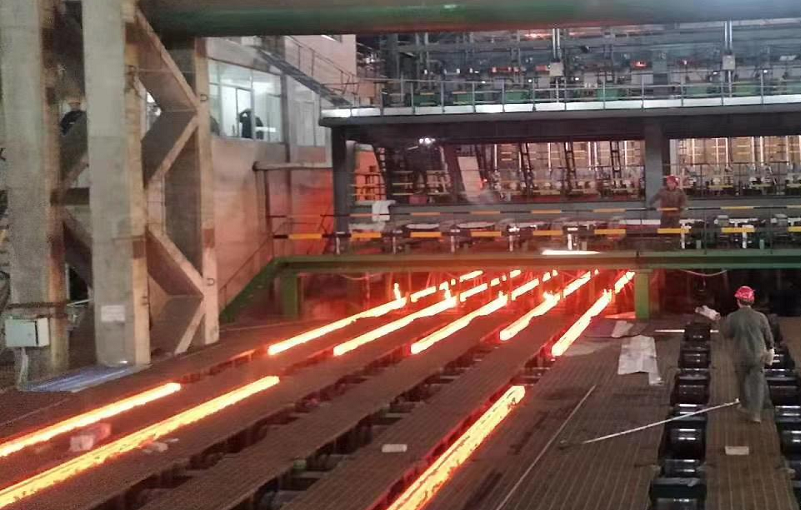