About Steel Rolling Mill Plant Construction
You only need to provide the site, the type of steel produced, and the annual production capacity (for example, a steel bar production line with an annual output of 200,000 tons), and we will take care of the rest. We will design the factory according to your needs, from civil engineering to overall layout, rolling mill selection, customized design, manufacturing, installation and commissioning, worker training, after-sales, etc., and finally deliver to you a steel rolling mill that can be put into production immediately.
Common Steel Rolling Mill Plant Production Line
Wire and bar rolling mills are in the greatest demand as the products they produce are the most widely used and common, and can effectively enhance the manufacturing and production capacity of local industries.
A steel rolling line with an annual output of 300,000 tons of Φ10-Φ40 bars.
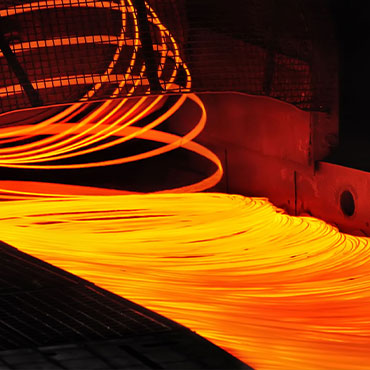
A wire rod rolling production line with an annual output of 200,000 tons.
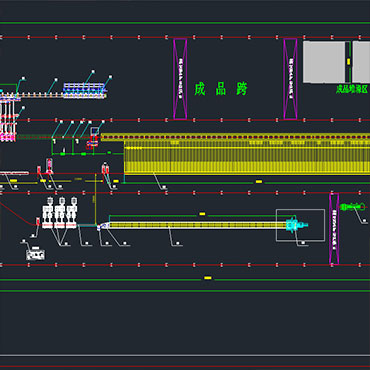
The factory is able to produce both rods and wires to meet the diverse needs of the market.
Strip and Plate Steel Rolling Mill Plant Production Lines
The market demand for strip steel and plate steel is also relatively large. HANI STEEL is also very good at these two types of rolling mill production lines and has many successful project cases.
Profile Rolling Mill Plant Production Line
Steel sections have a wide range of uses and types. With many years of experience in the metallurgical industry, HANI STEEL can provide professional custom design and manufacturing for your steel section rolling mill.
What Can the Steel Rolling Mill Plant We Built Produce?
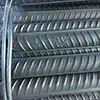
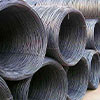
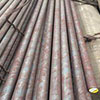
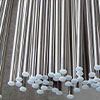
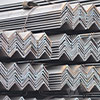
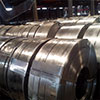
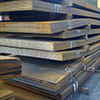
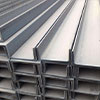
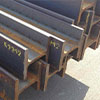
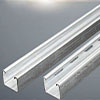
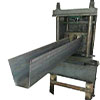
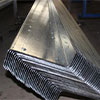
Rich Experience in Steel Rolling Mill Construction
“HANI STEEL has accumulated rich experience in steel rolling mill construction with many years of experience.
Currently, there are many steel rolling mill projects under construction and completed around the world.
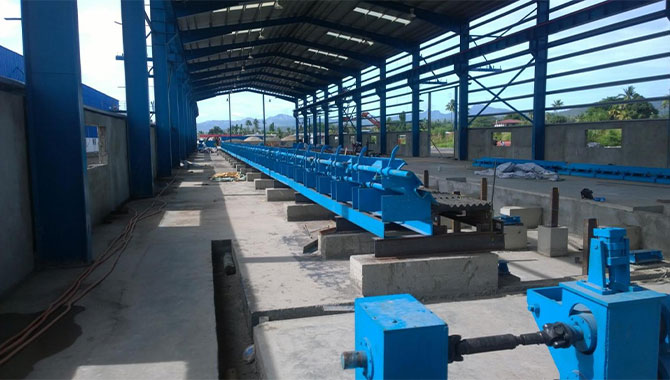
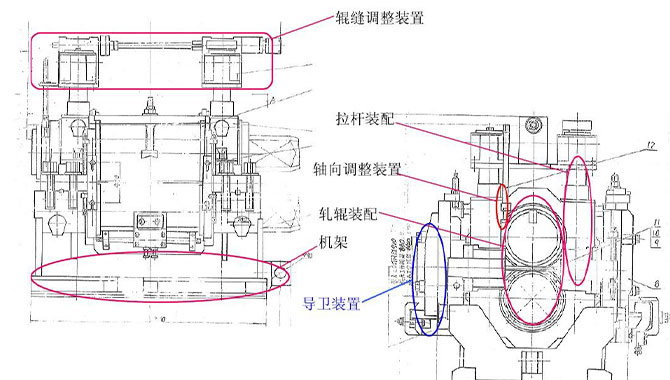
Professional Steel Rolling Mills Design Capabilities
“HANI STEEL has many experienced steel mill design engineers, all of whom have decades of experience in design and on-site production management.
From the early planning of the steel mill to the later production, they can make the best design and judgment.
HANI STEEL has close cooperation with many steel research institutions. Relying on China’s strong manufacturing capabilities, we can provide you with more complex and professional services.”
Advanced Manufacturing Capabilities
“Advanced manufacturing capabilities are the basis for us to provide better services to our customers. HANI STEEL has 26 years of manufacturing experience in equipment production for steel rolling mills.
HANI STEEL has introduced various advanced production equipment over the years. In order to better serve our customers, we moved our manufacturing center to the coastal city of Fujian, China in 2020.”
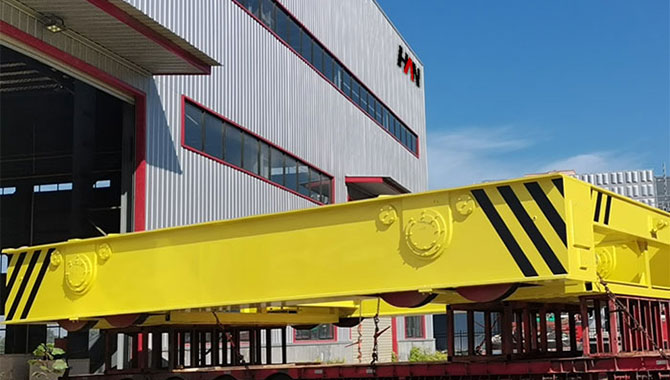
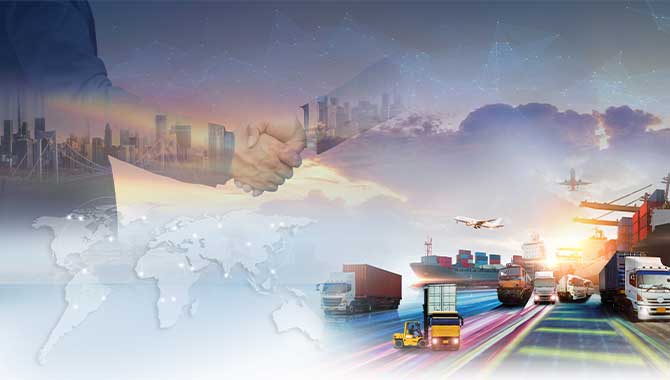
Global Services
We have 26 years of experience in steel mill construction.
Based on this experience, we deeply understand that it is very important to respond quickly to customer needs in steel mill construction.
So we have established branches in Istanbul, Dubai, Tehran, Yangon and Cameroon to better serve our customers.
Why Choose Us?
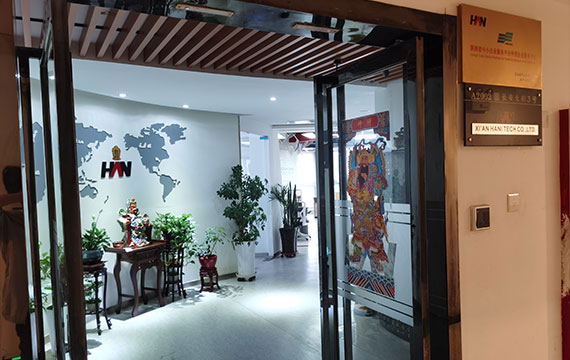
“HANI STEEL specializes in hot-rolled steel mill construction, integrating research and development, design, manufacturing and sales of steel mills.
We have many hot-rolled steel mill projects under construction and completed around the world, so we have accumulated rich experience in steel mill construction and can efficiently make feasible solutions that best meet user expectations;
The company has many experienced steel mill design engineers who can make the most reasonable design and solutions at all stages of the project;
The company’s advanced manufacturing equipment and rich manufacturing experience can also meet the diverse needs of customers.”
Main Equipment of Steel Rolling Mill
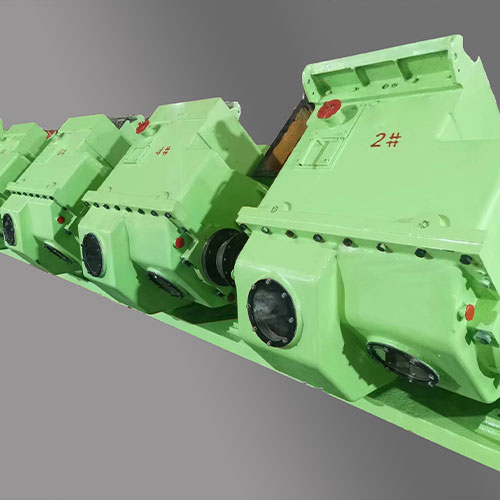
Mainly used in high-speed wire steel rolling mills
High precision: can accurately control the shape, size and surface quality of rolled products.
High efficiency and stability: high production efficiency and good equipment stability.
Intelligence: modern finishing mills are often intelligent, with automatic control and remote monitoring functions.
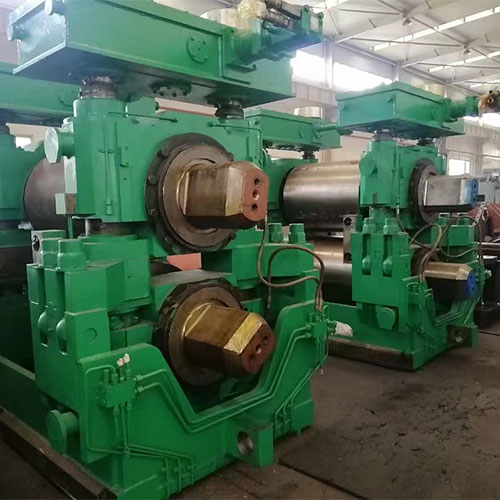
High efficiency: can roll steel quickly and continuously with high output.
Compact: small size, light weight, easy to install and maintain.
Safety: equipped with a variety of protection measures to ensure safe operation.
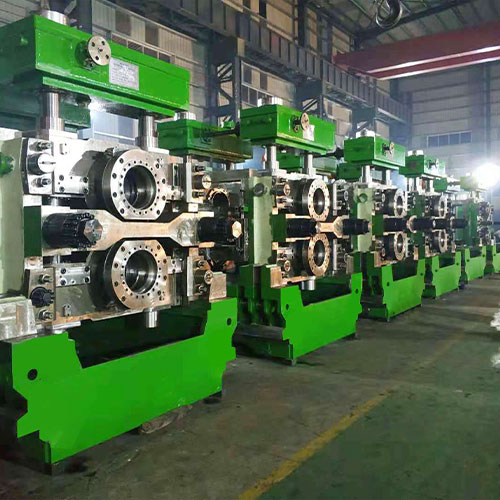
Multifunctional: It can roll various steels with complex cross-sections, such as H-beams, I-beams, etc.
Uniform deformation: The material deforms evenly during rolling, and the internal stress is small.
Flexible adjustment: The roll configuration and parameters are adjustable to adapt to different specifications of steel.
More Showcase
- Gallery
- High-speed steel rolling production line configuration
Specification | stand sstructure | Incoming material specification(mm) | Feed temperature(℃) |
84m/s No twist 45°side cross mill type | 8 stand smill unit | Φ16-19 | 900-1050 |
90m/s No twist 45°side cross mill type | 6 stand smill unit | Φ13-15 | 900-1050 |
135m/s top cross 45° no twist model | 8 stand smill unit | Φ13-19 | 900-1050 |
140m/stop cross 45° no twist model | 10 stand smill unit | Φ17-24 | 900-1050 |
Auxiliary Equipment and Spare Parts
What are the main energy-saving measures in steel rolling mills?
Mainly from the following points:
1. Optimize the process: adjust the rolling parameters to reduce unnecessary energy consumption.
2. Use energy-saving equipment: update or replace high-efficiency and energy-saving equipment.
3. Energy management: establish a monitoring system to reduce waste.
4. Waste heat recovery: use the waste heat generated during the rolling process.
5. Maintain equipment: ensure efficient operation of equipment and reduce failures.
6. Improve awareness: enhance employees’ energy-saving awareness and cultivate energy-saving habits.
In the early stage, you only need to provide the size of your site, the products you need to produce and the production capacity.
1. Products with similar specifications and sizes can share a production line, such as wire rods with similar specifications, bars with similar specifications, and strip steel with similar specifications, which can all be produced on a rolling line.
2. Similar products can share part of a production line, such as bars and wire rods can share the blanking machine part of the rolling line, and strip steel and plate steel with similar specifications can also share the blanking machine part of the rolling line.
3. Different products cannot use a rolling line, such as strip steel and H-shaped steel, angle steel and channel steel, and rebar and I-shaped steel.
For the whole line, our delivery cycle is generally 120 to 150 days.