Introduction to Steel Rolling Mills
A steel rolling mill is a critical industrial facility that processes raw steel into standardized shapes such as plates, sheets, bars, or coils. These mills utilize high-pressure rollers to deform and refine steel ingots or billets, achieving precise dimensions and improved mechanical properties. The process is central to industries like construction, automotive, and machinery manufacturing.
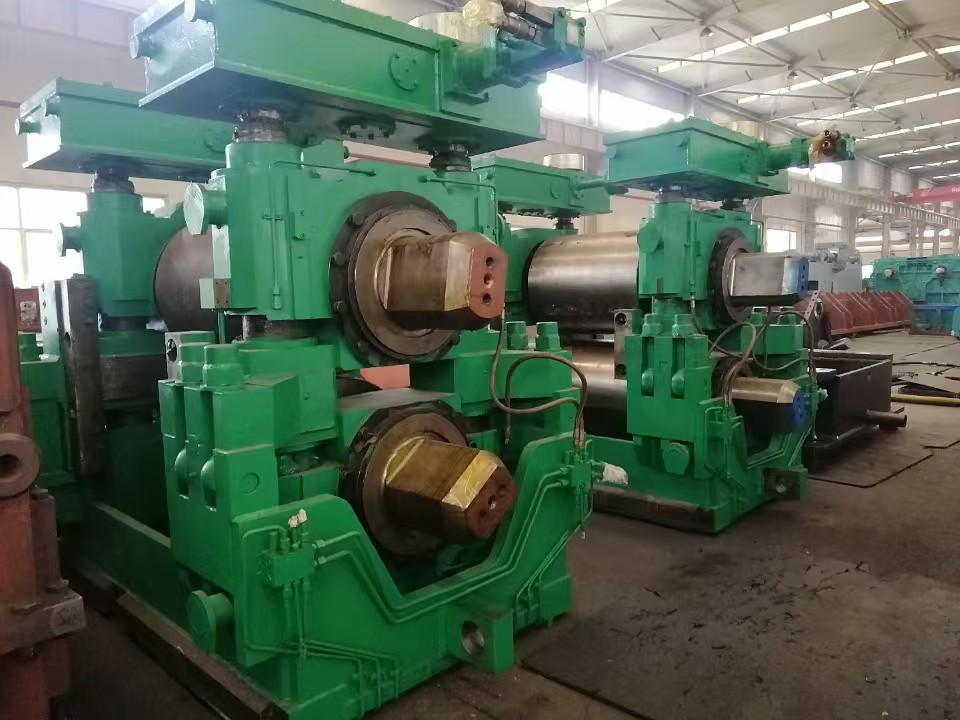
Types of Steel Rolling Mills
Hot Rolling Mills operate at temperatures above the steel’s recrystallization point (typically 1,100°C), enabling large-scale shaping with reduced energy consumption. Cold Rolling Mills, in contrast, process steel at room temperature to produce thinner gauges with superior surface finishes. Other variants include:
- Plate Mills: For heavy-duty steel plates used in shipbuilding.
- Rod Mills: Producing wire rods for cables and fasteners.
- Tube Mills: Manufacturing seamless or welded pipes.
Key Parameters of Steel Rolling Mills
Technical specifications define a rolling mill’s capabilities. Below is a detailed comparison of parameters for hot and cold rolling mills, incorporating data from HANI TECH and HANI Metallurgy:
Parameter | Hot Rolling Mill | Cold Rolling Mill |
---|---|---|
Roll Diameter (mm) | 800–1,400 | 400–700 |
Rolling Force (kN) | 20,000–45,000 | 8,000–25,000 |
Motor Power (kW) | 5,000–15,000 | 2,000–6,000 |
Maximum Speed (m/min) | 10–30 | 100–1,500 |
Thickness Tolerance (mm) | ±0.2–0.5 | ±0.01–0.05 |
Temperature Range (°C) | 900–1,250 | 20–150 |
Material Yield Strength (MPa) | 250–400 | 300–1,200 |
Annual Capacity (tons) | 500,000–5M | 100,000–1M |
Innovations by HANI TECH
HANI TECH specializes in high-performance rolling mills, integrating automation and predictive maintenance systems. Their smart rolling mills leverage IoT sensors to monitor roll wear and temperature in real-time, reducing downtime by 30%. Meanwhile, HANI Metallurgy focuses on energy-efficient designs, such as regenerative drives that recover braking energy, cutting power consumption by 15–20%.
Maintenance and Optimization
Regular upkeep of a steel rolling mill ensures longevity and precision. Critical practices include:
- Lubrication of roller bearings to minimize friction.
- Alignment checks to prevent uneven wear.
- Thermal imaging for early detection of stress cracks.
Future Trends in Rolling Technology
Emerging technologies like AI-driven process control and hybrid rolling (combining hot and cold stages) are reshaping the industry. HANI TECH’s R&D team is pioneering hydrogen-based annealing furnaces, aiming to reduce carbon emissions by 50% by 2030.
Conclusion
Modern steel rolling mills are marvels of engineering, blending brute force with microscopic precision. Companies like HANI TECH continue to push boundaries, ensuring these machines meet the demands of sustainable manufacturing. Whether optimizing parameters or adopting green technologies, the evolution of rolling mills remains pivotal to global industrialization.