Roll is an important part of the rolling mill in a steel plant. The pressure generated by a pair or group of rolls is used to roll the steel. It mainly bears the influence of dynamic and static load, wear and temperature change during rolling. The materials of work rolls in common cold rolls include 9Cr, 9Cr2, 9crv, 8crmov, etc. cold rolling surface quenching is required for the roller, and the hardness is hs45 ~ 105.
The commonly used materials of hot rolling roller include 55mn2, 55cr, 60CrMnMo, 60simnmo, etc. the hot rolling roll is used in the processing of billet, thick plate, section steel, etc. It bears the influence of strong rolling force, severe wear and thermal fatigue. Moreover, the hot roll works at high temperatures and allows the diameter wear within the unit workload. Therefore, it does not require surface hardness, but only high strength, toughness and heat resistance.
The hot rolling roller only adopts overall normalizing or quenching, and the surface hardness requires hb190 ~ 270 hardness. Roll hardness is an indirect physical value, which is affected by the internal structure of the roll itself, such as the matrix hardness of the roller material, the type and quantity of carbides in the roll material, the residual stress of the roll and so on; At the same time, because the commonly used shore and Leeb hardness tests for roll hardness testing are rebound hardness testing, they are greatly affected by the state of testing instruments, psychological factors of operators and other factors. Therefore, both the manufacturing and using departments of rolls need to assign special personnel to be responsible for hardness testing, pay attention to the selection of hardness tester, and the comparison relationship with other hardness should be stable. At the same time, pay attention to the frequent submission and calibration of hardness testing instruments and standard test blocks. Qualified enterprises can promote the use of standard rolls for hardness tester calibration.
In addition, pay attention to the use method during the use of the roll, otherwise it will bring loss and inconvenience to the production. In the rolling process, when the roll contacts with high-temperature rolling materials, it should bear rolling pressure, twisting force, mechanical impact, mechanical wear and thermal action. Improper handling will lead to roll fatigue and roll failure.
When using the roll, the diameter deviation of the upper and lower rolls shall be strictly in accordance with the requirements of 0.05-0.15mm. In this state, it can reduce the excessive instantaneous impact of the strip on the roll and protect the roll surface from damage. The rolling water cooling shall be uniform and continuous, and sufficient water shall be used to effectively cool the roll. During the rolling process, the maximum surface temperature of the roll shall not exceed 55 ℃, the maximum temperature of high chromium cast iron shall not exceed 60 ℃, and the maximum temperature of nickel chromium infinite chilled cast iron roll shall not exceed 65 ℃. Otherwise, the roll surface is prone to thermal fatigue or change the roll profile curve.
Various defects (mainly turtle cracks) on the roll surface must be removed before each production. The total amount of grinding for one-time use and repair of rolls (including wear, fatigue layer removal and roll profile repair) is generally 0.35-0.6mm. The total quantity of rolled products for each roll rolling should be 1800-2400 tons. Excessive rolling will cause excessive wear and deepening of microcracks, increase the amount of secondary grinding and increase the consumption of rolls. At the same time, it will also lead to a serious decline in plate quality (roughness, flatness, dimensional accuracy and thickness deviation).
In the rolling process, if the cooling water system fails, in order to avoid deep turtle cracks on the roll, the cold curved water flow should be closed as soon as possible; After the roll is off the machine, an all-round quality inspection shall be carried out to thoroughly grind off the surface defects such as turtle cracks. In addition, chilling and heating are strictly prohibited. Flaw detection shall be carried out on the roll regularly to check the quality of the roll surface, internal organization and bonding layer, so as to ensure that the roll can be used normally. It is recommended to match one with seven backup rolls to improve the anti accident risk of the roll.
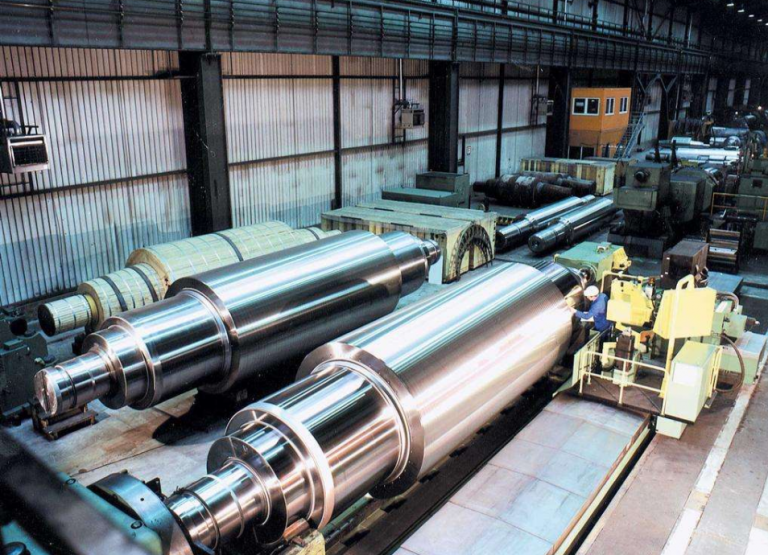