The induction furnace is an electric furnace that uses materials to induce electric heating effects to heat or melt materials.
The main components of the induction furnace are sensors, furnaces, power supplies, capacitors and control systems.
Under the action of the alternating electromagnetic field in the induction furnace, eddy currents are generated inside the material to achieve the effect of heating or melting. Under the stirring action of the alternating magnetic field, the composition and temperature of the material in the furnace are relatively uniform, the forging heating temperature can reach 1250 ° C, and the melting temperature can reach 1650 ° C.
In addition to being heated or smelted in the atmosphere, the induction furnace can be heated or smelted in a vacuum and a protective atmosphere such as argon or helium to meet special quality requirements.
Induction furnaces have outstanding advantages in diathermy or smelting soft magnetic alloys, high resistance alloys, platinum group alloys, heat resistant, corrosion-resistant, wear-resistant alloys, and pure metals. Induction furnaces are generally classified into induction heating furnaces and melting furnaces.
An electric furnace that heats material using an induced current generated by an induction coil. If the metal material is heated, it is placed in a crucible made of refractory material. If the non-metallic material is heated, the material is placed in a graphite crucible. When the AC frequency is increased, the induced current frequency is increased accordingly, and the amount of heat generated is increased. The induction furnace is heated quickly, the temperature is high, the operation and control are convenient, the material is less polluted during the heating process, and the product quality can be guaranteed. It is mainly used for melting special high-temperature materials, and also as a heating and control device for growing single crystals from the melt.
The melting furnace is divided into two types: a core induction furnace and a coreless induction furnace.
The core induction furnace has a core through the inductor and is powered by a commercial frequency power supply. It is mainly used for the melting and heat preservation of various cast iron, brass, bronze, zinc, and other metals. The electrical efficiency is over 90%, and the waste furnace can be used. The smelting cost is low, and the maximum furnace capacity is 270 tons.
The coreless induction furnace has no iron core passing through the inductor and is divided into a power frequency induction furnace, a triple frequency induction furnace, a generator set intermediate frequency induction furnace, a thyristor intermediate frequency induction furnace, and a high-frequency induction furnace.
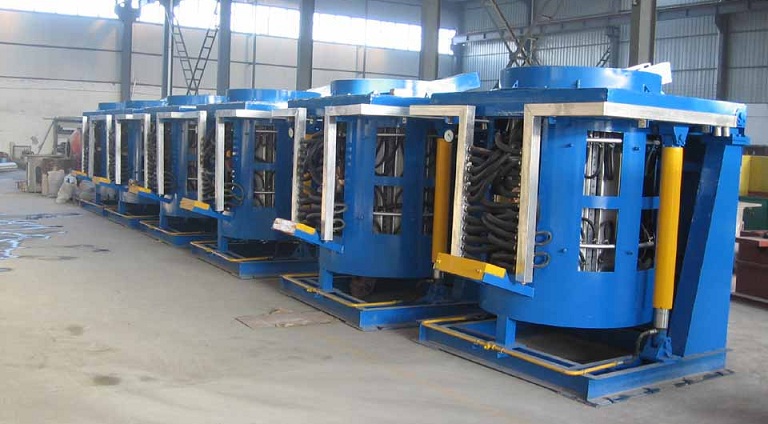