Wire Rod Rolling Steel Production Line(Annual production of 200,000 tons of Φ10mm-Φ18mm wire steel)
Product type: | Φ10-Φ18 wire steel |
---|---|
Annual output: | 200,000 tons |
Occupancy area: | 20,000㎡ |
Annual electricity consumption: | 15 million degrees |
Rolling mill configuration: | 5 ordinary rolling mills + 10 high-speed rolling mills |
Production speed: | 90m/s |
Qualified rate: | 90% or more |
Heating furnace: | Electromagnetic induction heating furnace |
Basic overview of wire rod rolling steel production line
The wire rod rolling steel plant mainly produces φ10-φ18 specification wire rod steel, with an annual designed production capacity of 200,000 tons. The plant covers an area of about 20,000 square meters. The plant has advanced production equipment and an efficient management system to ensure the high quality and stable supply of products.
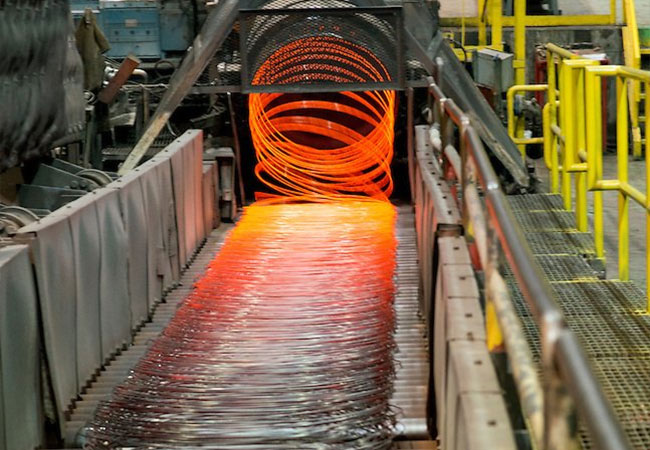
Main Equipment of Wire Rod Rolling Steel Production Line
Function: Continuously reduce the size of steel billets and prepare for finishing rolling.
Features: Combination of multiple rolling mills, high efficiency and strong adaptability.
Function: Finally rolled into wire products that meet the requirements.
Features: High precision, ensure product quality, the last link of the production line.
Function: Use electromagnetic induction to heat the billet to improve rolling efficiency.
Features: Rapid heating, good uniformity, energy saving and environmental protection.
Function: Cut the specified length on high-speed wire to ensure product length accuracy.
Features: High-speed shearing, high precision, easy operation.
- Why Choose us to Build a Wire Rod Rolling Steel Plant?
We have several wire rod rolling steel plant that have been completed and are under construction around the world, including rolling steel mill transformation and optimization projects.
These wire rod rolling steel plant projects have given us a deep accumulation in this field, enabling us to better serve our customers and solve their problems.
Core Equipment and Technology:
Wire rod rolling mills are the core equipment of the production line.
They use the latest rolling steel technology and can accurately control every detail of the rolling steel process to ensure that the diameter, surface finish and mechanical properties of the wire rod are in the optimal state.
At the same time, we also equip customers with electromagnetic induction heating furnaces dedicated to rolling steel. This advanced heating method not only improves heating efficiency, but also greatly reduces energy consumption and environmental pollution.
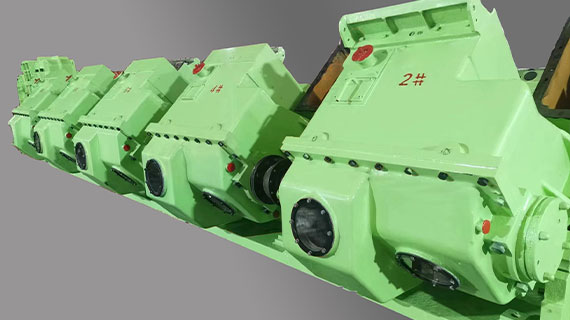
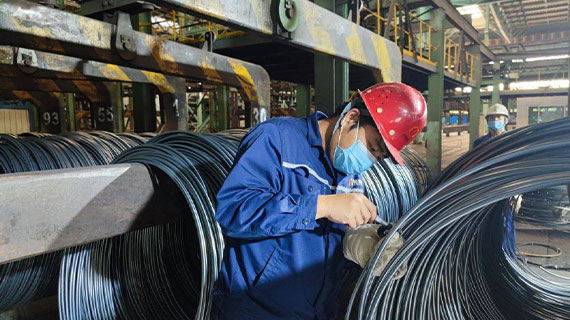
Quality Management and Environmental Protection:
We know that quality is the foundation of enterprise survival, so we have also established a strict quality management system for this wire rolling steel plant. From raw material procurement to finished product delivery, every link is strictly tested and controlled to ensure that the product qualification rate is always above 90%. In addition, we also actively advocate the concept of green production, and strive to achieve a win-win situation of economic benefits and environmental protection by optimizing the process of wire rolling steel production line, reducing energy consumption, reducing emissions and other measures.
Market and Service:
Φ10-Φ18 wire steel is widely used in many industries such as construction, machinery, and automobile manufacturing. In order to better serve customers, we can also do some market research, so that we can respond to market needs in a timely manner, provide personalized solutions and high-quality service support.
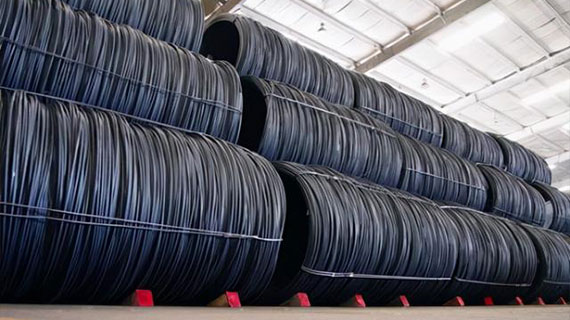
Wire Rod Rolling Steel Spare Parts
Spare parts are vital for wire rod rolling steel plant. They are the key to ensuring production continuity. Efficient spare parts management can quickly restore equipment operation, reduce production interruptions, optimize cost control, and ensure stable operation of the enterprise.
How can Wire Rod Rolling Steel Plant Save Costs?
Wire rod rolling steel mill needs to start from multiple aspects in terms of cost saving, especially to formulate specific measures and strategies based on the characteristics and actual situation of the wire rod rolling steel mill itself. The implementation and execution of these measures will help the wire rod rolling steel mill reduce production costs, improve economic benefits and market competitiveness.
Automated production: Promote the automation transformation of production lines, reduce labor costs, and improve production efficiency.
Intelligent control: Introduce intelligent control systems to achieve precise control of the production process and reduce scrap rates.
Process optimization: Conduct in-depth research and optimization of rolling processes to improve product quality and yield rate.
Technological innovation: Encourage technological innovation and research and development, and use new technologies and new materials to reduce production costs.
Generally speaking, a wire rod rolling production line can produce wire rods with diameters from 5mm to 25mm.
Yes, as long as the specifications are set, they can be produced.