The submerged arc furnace is used for the reduction smelting of metal oxide ore, so it is also called the submerged arc furnace.
When the submerged arc furnace is used to produce ferroalloy, it is called ferroalloy furnace; when it is used to produce calcium carbide, it is called calcium carbide furnace; when it is used to produce yellow phosphorus, it is called matte furnace; when it is used to refine ferroalloy, it is called submerged arc refining furnace; when it is used to melt pre-reduction furnace charge and separate metal from slag, it is called melting furnace.
For the submerged arc furnace, the refractory material masonry is also called furnace lining masonry. The molten pool of submerged arc furnace not only bears a strong high-temperature effect, but also is eroded and mechanically washed by furnace charge, high-temperature furnace gas, molten iron, and high-temperature slag, it is necessary to select specific refractory materials.
Requirements for refractory materials: high refractoriness, a large change in shape and volume at high temperature, high-temperature strength, good slag resistance, good chemical stability at high temperature, various refractory materials shall be kept clean in appearance, complete in structure, free of defects at corners and cracks on the surface.
In the masonry of the submerged arc furnace, the refractory materials for the submerged arc furnace are mainly refractory bricks, supplemented by refractory castables. The material selection is as follows:
1. Carbon brick
Carbon brick is a kind of carbon material. It is made of crushed coke and anthracite. Its specification is: Section 400mm × 400mm (allowable error ± 30mm), length 800~1600mm (allowable error ± 5mm);
The advantages of carbon brick are high fire resistance, strong thermal shock resistance, and high compressive strength; Good stability, especially volume stability and slag resistance. However, it is easy to oxidize at high temperatures, and the oxidation rate will accelerate with the increase in temperature.
Therefore, carbon materials cannot contact air, steam, and other gases at high temperatures. Carbon materials have high thermal conductivity and poor thermal insulation performance. In submerged arc furnaces, carbon bricks can be used as lining materials for all varieties that are not afraid of carburization. Self-baking carbon bricks are used for submerged arc furnaces.
2. Magnesia brick for submerged arc furnace
The main component of magnesia brick is magnesium oxide. Its refractoriness is above 2273k and its alkali resistance is very strong; however, the load softening point is low and the thermal shock resistance is poor. Most refining furnaces are smelted in an alkaline environment. Alkaline refractory materials resistant to alkaline corrosion should be selected, such as magnesia brick as lining.
3. Clay brick
Clay bricks are weak acid refractory materials, which can resist the erosion of acid slag. Refractory clay bricks cannot be used under high temperatures.
To sum up, the selection of refractories for submerged arc furnaces should be based on the actual smelting environment and smelting raw materials. High alumina bricks can also be used to replace clay bricks in the molten pool of a submerged arc furnace. In terms of performance, high alumina bricks have more advantages. Among the amorphous refractories, cold ramming paste and high alumina castables are the main ones.
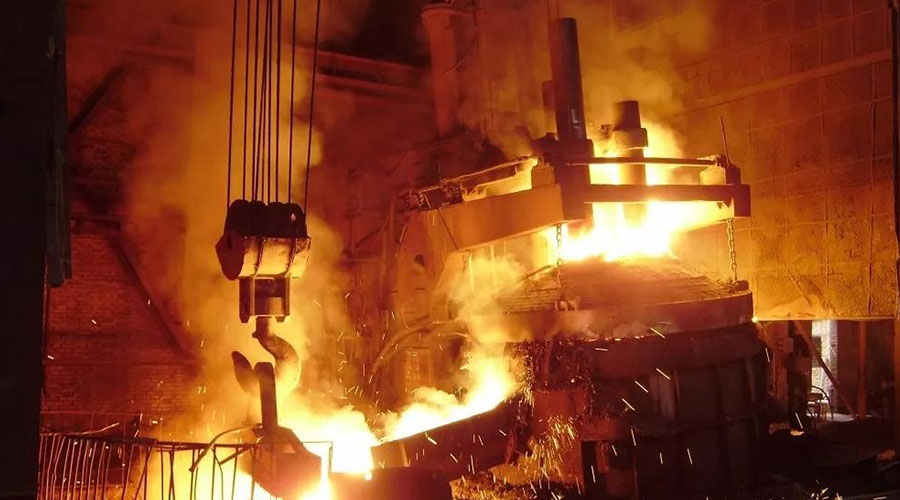