Causes of Surface Cracks in High-Speed Wire Rod Rolling Mill
Crack refers to the defect that the surface of the wire rod is straight or bent, bent or penetrated into the inside of wire rod at a certain angle along the rolling direction. Crack length and depth are different and can be found in the length direction of wire rod. Some cracks have inclusions and decarbonization on both sides.
The main reasons for surface cracks of wire rod out of high-speed wire rod rolling mill are that the uneliminated cracks (longitudinal or transverse), subcutaneous bubbles and non-metallic inclusions on the billet will cause cracks on the surface of wire rod. If the pinholes on the continuous casting slab are not eliminated, the linear hairlines of the finished products will be caused by the extension, oxidation, and dissolution after rolling. Pinhole is one of the most important defects in the continuous casting slab. It is difficult to detect pinhole when it is not exposed, and special attention should be paid to it. The cooling rate of high carbon steel wire rod after wire rod rolling mill rolling is too fast, which may also cause cracks in finished products, and the latter can also cause transverse cracks. Cracks formed by improper controlled cooling after rolling are not accompanied by decarbonization, and there is generally no oxide scale in the cracks. In addition, such problems may arise if the billet is not cleaned properly.
The main causes of cracks in the rolling process are as follows:
(1) The inappropriate groove is mainly due to the problem of sharp angle and groove size.
(2) Groove surface is too rough or damaged.
(3) Scratches of several guides before roughing rolling.
(4) Coarse iron oxide sheet is rolled into the surface and inside of the rolled piece, which usually occurs in the first few routes of roughing rolling.
(5) The main reason for the improper use of the guide is that the size is too large.
If a crack occurs, it should be checked from the following aspects to eliminate the failure:
(1) Whether high-pressure water descaling works normally, whether the cooling water of a rolling mill roll is blocked or deviated from the rolling groove.
(2) Whether the guide deviates from the wire rod rolling mill line or not, whether the oxide scale is blocked in a guide.
(3) Whether the groove is over-worn or damaged due to the handling of stacking accident.
(4) Whether the finishing mill has wrong rolls and whether the guide alignment and size correspond to the rolling specifications.
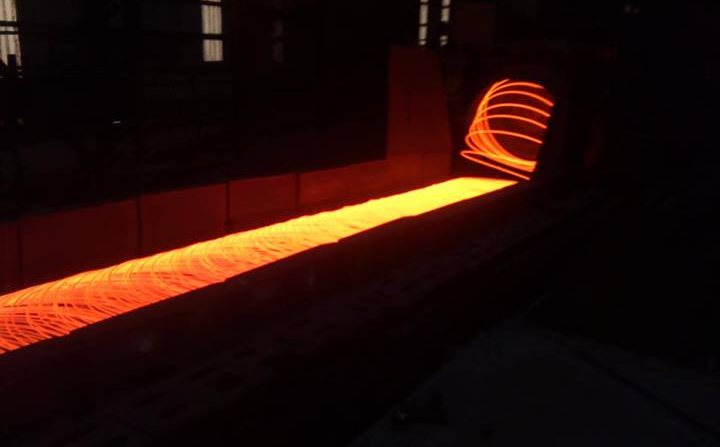