Introduction
The evolution of the industrial sector has been closely intertwined with advancements in metallurgical processes. Among these, the steel hot rolling mill stands out as a pivotal technology in transforming cast billets into usable steel products. This process not only enhances the mechanical properties of steel but also facilitates the production of high-quality rolled steel for diverse applications. In this article, we delve into the working principles, technical parameters, and market trends of the steel hot rolling mill, providing comprehensive insights for engineers, managers, and technical enthusiasts alike.
Historically, the development of the steel hot rolling mill has paralleled the growth of heavy industry. Modern improvements have elevated its performance through automation, real-time monitoring, and optimized control systems. By integrating innovative designs and precise rolling techniques, manufacturers can achieve superior surface quality, controlled microstructures, and enhanced strength properties. Additionally, the integration of digital monitoring systems and sensor-based diagnostics has further refined the rolling process, ensuring superior quality and efficiency in each production cycle.
Technical Principles and Process Overview
The fundamental concept behind a steel hot rolling mill involves heating steel billets to high temperatures and passing them through a series of rollers. The high temperature makes the steel malleable, allowing it to be reshaped through a series of reduction processes. As the material moves through various stands, the thickness is reduced while the length is increased, leading to a product with improved ductility and strength.
Key technical aspects of the steel hot rolling mill include:
- Temperature control: Maintaining optimal rolling temperatures to prevent scale formation and ensure uniform deformation.
- Roll pass design: Precise geometrical configuration of the rollers is essential for achieving the desired reduction and profile.
- Force and friction management: Efficient energy transfer is necessary to sustain the rolling process and ensure product consistency.
- Automation and monitoring: Real-time data acquisition systems are integrated to continuously adjust parameters, ensuring consistent product quality.
Advanced control systems, such as programmable logic controllers (PLCs) and distributed control systems (DCS), have revolutionized the steel hot rolling mill process. These systems provide instantaneous feedback and facilitate predictive maintenance, which collectively reduce downtime and enhance operational efficiency.
Integration of Digital Technologies
With the advent of Industry 4.0, the application of digital technologies has transformed the mechanics of the steel hot rolling mill. By installing internet-enabled sensors and devices, operators can now monitor various production parameters such as temperature, pressure, and strain in real time. Data analytics and machine learning algorithms are applied to optimize the rolling schedule, predict possible failures, and develop maintenance strategies.
This digital transformation also allows for improved resource management and energy efficiency. By analyzing historical production data and real-time sensor readings, manufacturers can better manage power consumption, reducing overall operational costs while minimizing environmental impact. The incorporation of digital twin technology further enables simulation of production scenarios, allowing for the testing of various rolling parameters without disrupting the actual production line.
Application Areas and Market Insights
The products generated via the steel hot rolling mill process are widely used across various industrial sectors, including automotive, construction, shipbuilding, and energy. The high-quality rolled steel produced not only offers enhanced structural characteristics but also meets the rigorous standards required by modern industries.
Moreover, organizations like HANI TECH have been instrumental in propagating technical know-how and marketing expertise regarding metallurgical equipment. Leveraging insights from platforms such as HANI TECH and HANI TECH Metallurgy, manufacturers and engineering professionals are better equipped to embrace technology-driven manufacturing methods. These platforms provide valuable information on the latest trends, cutting-edge designs, and performance benchmarks of the steel hot rolling mill and related equipment.
Market analysis indicates a rising demand for the technologically advanced steel hot rolling mill systems driven by stringent quality standards and increasing construction projects worldwide. As global demand for steel continues to grow, producers are encouraged to invest in modern rolling mills to improve productivity, product quality, and environmental sustainability.
Detailed Equipment Parameters and Table Overview
The performance of a steel hot rolling mill is gauged by several key parameters. Below is an extensive table summarizing the technical specifications and design features critical to the system’s operation. These parameters are essential for ensuring efficiency, quality, and operational safety. Manufacturers often refer to these detailed specifications to tailor the mill to specific production needs and material characteristics.
Parameter Category | Specification | Description |
---|---|---|
Rollers | Diameter | 500 mm – 1200 mm, providing optimal surface contact area. |
Material | High-alloy tool steel or cast iron lined with wear-resistant materials. | |
Number of Rolls | Typically 2 to 5 per stand, arranged in tandem. | |
Heat Treatment | Quenched and tempered for enhanced durability. | |
Heating System | Furnace Type | Walking beam or pusher type furnaces, ensuring uniform temperature distribution. |
Heating Temperature | 1100°C – 1300°C to achieve optimal malleability. | |
Fuel Type | Natural gas, oil, or electricity with selective energy recovery systems. | |
Insulation | High-temperature refractory materials for energy efficiency. | |
Cycle Time | 3 - 10 hours, depending on billet size and production volume. | |
Mechanical System | Drive System | Electric or hydraulic drives equipped with frequency converters. |
Rolling Force | Up to 50 MN (meganewtons) for high-load operations. | |
Speed Range | 0.1 m/s – 10 m/s adjustable speed control. | |
Reduction Ratio | 10% - 80% per pass, optimized for different sections of the mill. | |
Tension Control | Automatically adjusted using load sensors. | |
Lubrication | Advanced oil circulation systems to minimize friction and wear. | |
Control System | Automation Level | Fully integrated with PLC and DCS systems. |
Interface | Graphical user interface (GUI) and real-time monitoring software. | |
Data Logging | Continuous data recording for process optimization. | |
Remote Access | Enables diagnostics and maintenance using IoT devices. | |
Quality Assurance | Surface Quality | Controlled via precision roll adjustments and cooling systems. |
Dimensional Accuracy | Tolerance levels within ±0.5 mm for final product dimensions. | |
Material Homogeneity | Uniform grain structure achieved through controlled rolling sequences. | |
Inspection Techniques | Ultrasonic testing, eddy current inspection, and laser profiling. | |
Energy Management | Power Consumption | Optimized drive systems reduce consumption by up to 15%. |
Heat Recovery | Integrated systems capture waste heat for preheating billets. | |
Environmental Emissions | Compliant with international emission standards. |
The detailed parameters listed in the table above underscore the complexity and precision required during the operation of a steel hot rolling mill. Each category, from the rollers to energy management, plays a critical role in ensuring that the final rolled products meet stringent quality standards and performance benchmarks.
Advancements and Future Trends
As industries continue to evolve, the steel hot rolling mill is also witnessing significant innovations. Research and development initiatives are focusing on:
- Smart Manufacturing: The integration of advanced sensors and IoT devices enables intelligent process control, predictive maintenance, and real-time optimization.
- Energy Efficiency: Ongoing improvements in thermal insulation, furnace design, and waste heat recovery are critical for reducing operational costs and environmental impacts.
- Enhanced Automation: Automation levels are steadily rising, allowing for seamless production cycles with minimal human intervention, reducing error margins, and ensuring consistent product quality.
- Digital Twin Technology: Virtual simulations of the mill allow for testing of various production scenarios without the need for disruptive physical trials, thus enabling rapid innovation and process improvement.
- Material Innovation: New steel alloys and composite materials require modified rolling parameters, prompting continuous adaptation in mill design and operation strategies.
The global market continues to demand high-performance steel produced by advanced steel hot rolling mill facilities. Research laboratories and industrial experts across the world are working on further enhancing the corrosion resistance, tensile strength, and thermal stability of rolled steel. Collaboration between academia and industry is fostering improvements in software algorithms to better predict outcomes, and experimental setups are being established to push the boundaries of current technologies.
One noteworthy trend is the increasing integration of renewable energy sources within production facilities. Plants are adopting solar, wind, and combined heat and power (CHP) systems to reduce the carbon footprint and ensure sustainability. By leveraging data from platforms like HANI TECH, companies are making informed decisions to balance operational efficiency with environmental responsibility, ensuring that the steel hot rolling mill remains a leader in eco-friendly manufacturing practices.
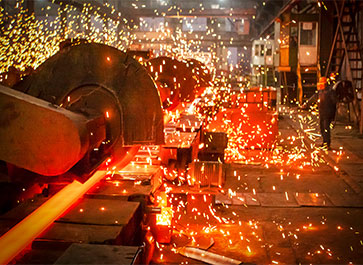
Economic and Strategic Implications
The economic impact of modernizing the steel hot rolling mill is significant. Adopting state-of-the-art technologies not only increases production capacity but also enhances the quality of the final product, which is crucial in competitive global markets. The capital investment in upgrading rolling mills is often offset by the reduction in maintenance downtime, energy savings, and increased demand for higher-grade steel products.
Companies investing in advanced rolling mill technology are better positioned to meet market demands for high-performance, durable, and cost-effective steel. As global infrastructure projects surge and automotive industries demand lighter yet stronger materials, the importance of having a modern steel hot rolling mill facility becomes more apparent. Enhanced data analytics and process optimization facilitate better market forecasting and strategic planning, enabling manufacturers to adapt swiftly to the evolving requirements of the steel industry.
Furthermore, policy initiatives and international standards are increasingly emphasizing sustainability and quality control. This regulatory environment pushes manufacturers to adopt more robust quality assurance protocols, which in turn stimulates further innovation in mill design and operation. The convergence of robust engineering practices, advanced digital technologies, and strategic market positioning is setting a new benchmark for the capabilities of a modern steel hot rolling mill.
Challenges and Mitigation Strategies
Despite the impressive advancements, the operation of a steel hot rolling mill faces several challenges. High energy consumption, thermal management issues, and severe mechanical wear in high-stress components can impede operational efficiency. Moreover, process fluctuations due to inconsistent raw material quality or external disruptions might lead to variations in product quality.
To address these challenges, manufacturers are implementing several mitigation strategies:
- Enhanced Monitoring: Implementing real-time monitoring systems allows operators to detect anomalies early and take corrective action promptly.
- Preventive Maintenance: Scheduled maintenance, combined with predictive analytics, helps in minimizing unexpected downtimes and prolongs the lifespan of key components.
- Process Optimization: Continuous research into roll pass design, cooling methodologies, and friction reduction technologies ensures that the steel hot rolling mill maintains consistency in product quality.
- Quality Control Automation: Advancements in sensor technology and imaging systems provide superior inspection techniques, ensuring that any defects in the rolled steel are detected and rectified during production.
Industry collaboration, supported by research initiatives from institutions and organizations such as HANI TECH, is fostering an environment where challenges are systematically addressed, and best practices are disseminated globally. Through collaborative platforms, manufacturers not only share technical insights but also adopt common standards that enhance product reliability and safety in the steel hot rolling mill process.
Conclusion
ال steel hot rolling mill is a cornerstone of modern steel production technology. It embodies the intersection of traditional metallurgical expertise and modern digital innovations, ensuring that steel products are manufactured with exceptional quality and efficiency. From advanced automation to sophisticated process control systems, the continuous evolution of the mill’s design reflects the industry’s commitment to excellence.
As demonstrated by the extensive technical parameters and process optimizations discussed in this article, the future of the steel hot rolling mill is bright. With ongoing investments in digital twin technology, sustainable energy practices, and state-of-the-art quality assurance methodologies, manufacturers are set to overcome current challenges and pave the way for further innovations in steel production.
In summary, the integration of cutting-edge research, empirical data, and advanced production strategies is redefining the capabilities of the steel hot rolling mill in today’s competitive industrial landscape. Engineers, decision-makers, and stakeholders are encouraged to harness the knowledge and insights provided here—augmented by the resources available at HANI TECH’s platforms (هاني TECH and HANI TECH Metallurgy)—to drive future growth and technological progress.
By continuously evolving and embracing innovation, the steel hot rolling mill will undoubtedly continue to be an indispensable asset in the metallurgical and heavy industries. It not only enhances the quality of steel products but also fortifies the competitive edge of manufacturers striving for excellence in an increasingly demanding global market.
Ultimately, whether you are an industry veteran or a newcomer, understanding the intricacies of the steel hot rolling mill process and its associated technologies is crucial. This knowledge empowers you to make informed decisions about production, investment, and strategic planning. Embracing these advanced technologies and operational best practices, as highlighted in this article, positions companies not only to meet the challenges of today but also to innovate for the future—a future where high-quality steel serves as the backbone of infrastructure and modern industry.
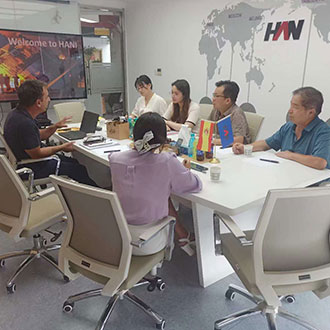
NOTE:
If you want to know more about the knowledge related to electric arc furnaces in the steel rolling industry and other aspects, please follow HANI’s YouTube channel for more information.
https://www.youtube.com/channel/UCQ5eAP3i7BddUh6VEQAePGA
https://www.youtube.com/@kevinqian8976/featured
https://www.youtube.com/channel/UCyQRZqd-TpcNO6iRTjY-cDQ